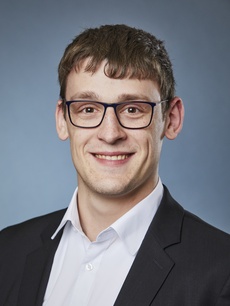
Maximilian Frey, M.Sc.
- Research Associate
- department: Manufacturing and Materials Technology
- office hours: to be agreed
- room: 128, Geb. 50.36
- phone: +49 1523 9502594
- fax: +49 721 608-45004
- maximilian frey ∂does-not-exist.Kit edu
- ORCID
Gotthard-Franz-Straße 5
76131 Karlsruhe
Maximilian Frey, M.Sc.
Area of Research:
- Additive manufacturing
Projects:
- AddPEM: Additive Fertigung von gradierten Strömungsstrukturen für PEM-Brennstoffzellen
- AddFlow: Strömungsangepasste Komponenten für Brennstoffzellen durch additiv-subtraktive Fertigung mit gezielt einstellbarer Oberflächenfunktion (hydrophob, hydrophil)
Curriculum Vitae:
since 05/2022 |
Research Associate at the Institute of Production Science (wbk) at Karlsruhe Institute of Technology (KIT) |
04/2020-04/2022 |
Master’s degree in mechanical engineering at Karlsruhe Institute of Technology (KIT) |
10/2016-03/2020 |
Bachelor’s degree in mechanical engineering at Karlsruhe Institute of Technology (KIT) |
Publications
Influence of Novel Space Filling PBF-LB Scanning Strategies on Part Distortion and Density
Frey, M.; Frankenhauser, M.; Schulze, V.; Zanger, F.
2024. Proceedings of the 35th Annual International Solid Freeform Fabrication Symposium. Ed.: J. Beaman, 720–731, University of Texas at Austin. doi:10.26153/tsw/58109
Frey, M.; Frankenhauser, M.; Schulze, V.; Zanger, F.
2024. Proceedings of the 35th Annual International Solid Freeform Fabrication Symposium. Ed.: J. Beaman, 720–731, University of Texas at Austin. doi:10.26153/tsw/58109
Thermomechanical multiscale PBF-LB-process simulation of macroscopic structures to predict part distortion recoater collisions
Drechsel, K.; Frey, M.; Schulze, V.; Zanger, F.
2022. M. Liewald, A. Verl, T. Bauernhansl & H.-C. Möhring (Eds.), Production at the Leading Edge of Technology Hrsg.: Liewald, Matthias; Verl, Alexander; Bauernhansl, Thomas; Möhring, Hans-Christian. Proceedings of the 12th Congress of the German Academic Association for Production Technology (WGP) Stuttgart, Deutschland, 12.10.2022–13.10.2022, 366–375, Springer. doi:10.1007/978-3-031-18318-8_38
Drechsel, K.; Frey, M.; Schulze, V.; Zanger, F.
2022. M. Liewald, A. Verl, T. Bauernhansl & H.-C. Möhring (Eds.), Production at the Leading Edge of Technology Hrsg.: Liewald, Matthias; Verl, Alexander; Bauernhansl, Thomas; Möhring, Hans-Christian. Proceedings of the 12th Congress of the German Academic Association for Production Technology (WGP) Stuttgart, Deutschland, 12.10.2022–13.10.2022, 366–375, Springer. doi:10.1007/978-3-031-18318-8_38
Thermal insulation and laser-based preheating method for processing a ledeburitic tool steel in LPBF
Graf, G.; Leoni, M.; Müller, T.; Fischer-Bühner, J.; Frey, M.; Beckers, D.; Donisi, S.; Zanger, F.; Schulze, V.
2020. Holistic innovation in Additive Manufacturing
Graf, G.; Leoni, M.; Müller, T.; Fischer-Bühner, J.; Frey, M.; Beckers, D.; Donisi, S.; Zanger, F.; Schulze, V.
2020. Holistic innovation in Additive Manufacturing