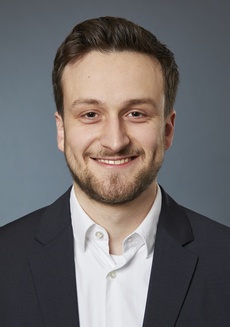
Alexander Puchta, M.Sc.
- Oberingenieur Intelligente Maschinen und Komponenten
- Bereich: Maschinen, Anlagen und Prozessautomatisierung
- Sprechstunden: nach Vereinbarung
- Raum: 013, Geb. 70.16
- Tel.: +49 1523 9502627
- alexander puchta ∂does-not-exist.kit edu
76131 Karlsruhe
Kaiserstraße 12
Alexander Puchta, M.Sc.
Forschungs- und Arbeitsgebiete:
- Themenbereich Industrie 4.0
- Automatisierung der spanenden Fertigung
- Automatisierte Modellierung von Vorschubachsen
Projekte:
- SDM4FZI - Digitalisierung von Brownfield-Produktionsanlagen für Software-defined Manufacturing
- ProKI Karlsruhe - Karlsruher Zentrum für KI in der Zerspanung
- BatterI4.0 - Leitfaden zur Digitalisierung der Batteriezellproduktion
Lebenslauf:
seit 01/2023 | Leiter der Gruppe Intelligente Maschinen und Komponenten |
seit 07/2020 |
Wissenschaftlicher Mitarbeiter am Institut für Produktionstechnik (wbk) des Karlsruher Instituts für Technologie (KIT) |
Veröffentlichungen
PyBullet Industrial Path Planner: Handling Transitional Movements in Constrained Robot Cell Environments
Schulz, P.; Hansjosten, M.; Puchta, A.; Fleischer, J.
2025. Karlsruher Institut für Technologie (KIT). doi:10.5445/IR/1000183537
Schulz, P.; Hansjosten, M.; Puchta, A.; Fleischer, J.
2025. Karlsruher Institut für Technologie (KIT). doi:10.5445/IR/1000183537
From Toy Problems to Industrial Reality: The wbk Assembly Benchmark
Baumgärtner, J.; Kreft, L.; Puchta, A.; Fleischer, J.
2025, Juli 3. doi:10.35097/3c5yh8z8asafagby
Baumgärtner, J.; Kreft, L.; Puchta, A.; Fleischer, J.
2025, Juli 3. doi:10.35097/3c5yh8z8asafagby
A Multimodal Dataset for Process Monitoring and Anomaly Detection in Industrial CNC Milling
Ströbel, R.; Kuck, M.; Oexle, F.; Kader, H.
2025, Juli 1. doi:10.35097/hvvwn1kfwf7qt48z
Ströbel, R.; Kuck, M.; Oexle, F.; Kader, H.
2025, Juli 1. doi:10.35097/hvvwn1kfwf7qt48z
Assistenzsystem für effiziente Maschinenabnahme/Classifying deviations in test workpieces and optimizing control parameters – Worker Assistance for Machine Acceptance
Frisch, M.; Ströbel, R.; Puchta, A.; Fleischer, J.
2025. Werkstattstechnik, 115 (5), 321–325. doi:10.37544/1436-4980-2025-05-11
Frisch, M.; Ströbel, R.; Puchta, A.; Fleischer, J.
2025. Werkstattstechnik, 115 (5), 321–325. doi:10.37544/1436-4980-2025-05-11
Hybrid Machine Learning for CNC Process Monitoring
Ströbel, R.; Deucker, S.; Zhou, H.; Kader, H.; Puchta, A.; Noack, B.; Fleischer, J.
2025. IEEE Access, 13 (1), 91875–91888. doi:10.1109/ACCESS.2025.3573400
Ströbel, R.; Deucker, S.; Zhou, H.; Kader, H.; Puchta, A.; Noack, B.; Fleischer, J.
2025. IEEE Access, 13 (1), 91875–91888. doi:10.1109/ACCESS.2025.3573400
Modellbasierte Überwachung von Fräsprozessen - Zustandsspezifische Modelle zur universellen Prozessüberwachung
Mau, M.; Puchta, A.; Fleischer, J.
2025. wt Werkstattstechnik online, 115 (05), 316–320. doi:10.37544/1436-4980-2025-05-6
Mau, M.; Puchta, A.; Fleischer, J.
2025. wt Werkstattstechnik online, 115 (05), 316–320. doi:10.37544/1436-4980-2025-05-6
Part series dataset of milling processes for time series prediction
Ströbel, R.; Kader, H.; Mau, M.; Deucker, S.; Bless, D.; Oexle, F.
2025, April 9. doi:10.35097/ctvuj6dgzepzmk0g
Ströbel, R.; Kader, H.; Mau, M.; Deucker, S.; Bless, D.; Oexle, F.
2025, April 9. doi:10.35097/ctvuj6dgzepzmk0g
Extended Intelligence for Rapid Cognitive Reconfiguration
Mayer, A.; Otto, S.; Chardonnet, J.-R.; Puchta, A.; Fleischer, J.; Ovtcharova, J.
2025. Zeitschrift für wirtschaftlichen Fabrikbetrieb, 120 (s1), 177–180. doi:10.1515/zwf-2024-0159
Mayer, A.; Otto, S.; Chardonnet, J.-R.; Puchta, A.; Fleischer, J.; Ovtcharova, J.
2025. Zeitschrift für wirtschaftlichen Fabrikbetrieb, 120 (s1), 177–180. doi:10.1515/zwf-2024-0159
Lean Data – Anwendungsspezifische Reduktion großer Datenmengen im Produktionsumfeld
Baucks, M.; Mau, M.; Ruppelt, P.; Puchta, A.; Fleischer, J.
2025. Zeitschrift für wirtschaftlichen Fabrikbetrieb, 120 (s1), 152–158. doi:10.1515/zwf-2024-0148
Baucks, M.; Mau, M.; Ruppelt, P.; Puchta, A.; Fleischer, J.
2025. Zeitschrift für wirtschaftlichen Fabrikbetrieb, 120 (s1), 152–158. doi:10.1515/zwf-2024-0148
Intelligente Prozessüberwachung für die flexible Produktion – Integration von Physics-Informed Machine Learning und Active Learning
Ströbel, R.; Kader, H.; Hutt, L.; Zhou, H.; Mau, M.; Puchta, A.; Noack, B.; Fleischer, J.
2025. Zeitschrift für wirtschaftlichen Fabrikbetrieb, 120 (s1), 224–231. doi:10.1515/zwf-2024-0154
Ströbel, R.; Kader, H.; Hutt, L.; Zhou, H.; Mau, M.; Puchta, A.; Noack, B.; Fleischer, J.
2025. Zeitschrift für wirtschaftlichen Fabrikbetrieb, 120 (s1), 224–231. doi:10.1515/zwf-2024-0154
Novel Processes for the Production of Continuous Carbon Fiber-Reinforced Thermoplastic Polymers via Additive Manufacturing and Comparisons
Zeidler, S.; Matkovic, N.; Kößler, F.; Puchta, A.; Fleischer, J.
2025. Polymers, 17 (5), Art.-Nr.: 584. doi:10.3390/polym17050584
Zeidler, S.; Matkovic, N.; Kößler, F.; Puchta, A.; Fleischer, J.
2025. Polymers, 17 (5), Art.-Nr.: 584. doi:10.3390/polym17050584
Sensorless tool wear estimation by using the artificial intelligence (AI) tools from the currents of motors generating linear motions
Demetgul, M.; Darji, A. R.; Tansel, I. N.; Puchta, A.; Fleischer, J.; Stork, W.
2025. The International Journal of Advanced Manufacturing Technology, 136 (10), 4335–4353. doi:10.1007/s00170-025-15069-x
Demetgul, M.; Darji, A. R.; Tansel, I. N.; Puchta, A.; Fleischer, J.; Stork, W.
2025. The International Journal of Advanced Manufacturing Technology, 136 (10), 4335–4353. doi:10.1007/s00170-025-15069-x
Beyond proxies: A direct time-optimal approach to robot cell layout optimization
Baumgärtner, J.; Puchta, A.; Fleischer, J., (1)
2025. CIRP Annals, 74 (1), 19–23. doi:10.1016/j.cirp.2025.04.079
Baumgärtner, J.; Puchta, A.; Fleischer, J., (1)
2025. CIRP Annals, 74 (1), 19–23. doi:10.1016/j.cirp.2025.04.079
Developing a Concept for an OPC UA Standard to Improve Interoperability in Battery Cell Production: A Methodological Approach for Standardization in Heterogeneous Production Environments
Sawodny, J.; Otte, S.; Böttinger, F.; Haag, F.; Schlereth, A.; Hülsmann, T.-H.; Tidde, F.; Roth, D.; Schmetz, A.; Puchta, A.; Schabel, S.; Bauernhansl, T.; Fleischer, J.
2025. Technologies, 13 (7), Article no: 302. doi:10.3390/technologies13070302
Sawodny, J.; Otte, S.; Böttinger, F.; Haag, F.; Schlereth, A.; Hülsmann, T.-H.; Tidde, F.; Roth, D.; Schmetz, A.; Puchta, A.; Schabel, S.; Bauernhansl, T.; Fleischer, J.
2025. Technologies, 13 (7), Article no: 302. doi:10.3390/technologies13070302
Laser Tracker Placement Optimization for Highly Flexible Manufacturing Systems
Goebels, M.; Baumgärtner, J.; Puchta, A.; Fleischer, J.
2025. Production at the Leading Edge of Technology. Ed.: W.-G. Drossel, 334–341, Springer Nature Switzerland. doi:10.1007/978-3-031-86893-1_37
Goebels, M.; Baumgärtner, J.; Puchta, A.; Fleischer, J.
2025. Production at the Leading Edge of Technology. Ed.: W.-G. Drossel, 334–341, Springer Nature Switzerland. doi:10.1007/978-3-031-86893-1_37
Optimization of Adversarial Reprogramming for Transfer Learning on Closed Box Models
Bott, A.; Siems, M.; Puchta, A.; Fleischer, J.
2025. IEEE Access, 13, 48999–49006. doi:10.1109/ACCESS.2025.3552219
Bott, A.; Siems, M.; Puchta, A.; Fleischer, J.
2025. IEEE Access, 13, 48999–49006. doi:10.1109/ACCESS.2025.3552219
Automated Detection of Disassembly States in Electric Motors Using Point Cloud Comparison
Hansjosten, M.; Kretschmer, J.; Puchta, A.; Fleischer, J.
2024. Proceedings of the 14th International Electric Drives Production Conference (EDPC), Article no: 45870, Institute of Electrical and Electronics Engineers (IEEE). doi:10.1109/EDPC63771.2024.10932841
Hansjosten, M.; Kretschmer, J.; Puchta, A.; Fleischer, J.
2024. Proceedings of the 14th International Electric Drives Production Conference (EDPC), Article no: 45870, Institute of Electrical and Electronics Engineers (IEEE). doi:10.1109/EDPC63771.2024.10932841
Finding Predictive Features for Energy Consumption of CNC Machines
Kader, H.; Ströbel, R.; Puchta, A.; Fleischer, J.; Noack, B.; Spiliopoulou, M.
2024. GFaI Tagungsband 2024. Hrsg.: A. Iwainsky, 89–95, Gesellschaft zur Förderung der Abwassertechnik (GFA)
Kader, H.; Ströbel, R.; Puchta, A.; Fleischer, J.; Noack, B.; Spiliopoulou, M.
2024. GFaI Tagungsband 2024. Hrsg.: A. Iwainsky, 89–95, Gesellschaft zur Förderung der Abwassertechnik (GFA)
Efficient Deployment of Machine Learning Models in Manufacturing and Industrial Environments using ROS
Frisch, M.; Baumgärtner, J.; Heider, I.; Puchta, A.; Fleischer, J.
2024. Procedia CIRP, 130, 188–193. doi:10.1016/j.procir.2024.10.074
Frisch, M.; Baumgärtner, J.; Heider, I.; Puchta, A.; Fleischer, J.
2024. Procedia CIRP, 130, 188–193. doi:10.1016/j.procir.2024.10.074
Automated Identification of Components of Feed Axes
Puchta, A.; Frisch, M.; Fleischer, J.
2024. Production at the Leading Edge of Technology. Hrsg.: T. Bauernhansl, 143–151, Springer Nature Switzerland. doi:10.1007/978-3-031-47394-4_15
Puchta, A.; Frisch, M.; Fleischer, J.
2024. Production at the Leading Edge of Technology. Hrsg.: T. Bauernhansl, 143–151, Springer Nature Switzerland. doi:10.1007/978-3-031-47394-4_15
Machine Learning-Driven RUL Prediction and Uncertainty Quantification for Ball Screw Drives in a Cloud-Ready Maintenance Framework
Bott, A.; Liu, B.; Puchta, A.; Fleischer, J.
2024. Journal of Machine Engineering, 24 (3), 17 – 31. doi:10.36897/jme/192681
Bott, A.; Liu, B.; Puchta, A.; Fleischer, J.
2024. Journal of Machine Engineering, 24 (3), 17 – 31. doi:10.36897/jme/192681
One Problem, One Solution: Unifying Robot Design and Cell Layout Optimization
Baumgärtner, J.; Puchta, A.; Fleischer, J.
2024. 2024 IEEE/RSJ International Conference on Intelligent Robots and Systems (IROS), Abu Dhabi, 14th-18th October 2024, 2292–2298, Institute of Electrical and Electronics Engineers (IEEE). doi:10.1109/IROS58592.2024.10801417
Baumgärtner, J.; Puchta, A.; Fleischer, J.
2024. 2024 IEEE/RSJ International Conference on Intelligent Robots and Systems (IROS), Abu Dhabi, 14th-18th October 2024, 2292–2298, Institute of Electrical and Electronics Engineers (IEEE). doi:10.1109/IROS58592.2024.10801417
Jacobian-Sensitivity Approach for Identifying Machine Dynamic Model Parameters of Robots with Flexible Joints
Oexle, F.; Benfer, A.; Puchta, A.; Fleischer, J.
2024. Procedia CIRP - 10th CIRP Conference on Assembly Technology and Systems (CIRP CATS 2024), 127, 116–121. doi:10.1016/j.procir.2024.07.021
Oexle, F.; Benfer, A.; Puchta, A.; Fleischer, J.
2024. Procedia CIRP - 10th CIRP Conference on Assembly Technology and Systems (CIRP CATS 2024), 127, 116–121. doi:10.1016/j.procir.2024.07.021
Feature Ranking for the Prediction of Energy Consumption on CNC Machining Processes
Kader, H.; Ströbel, R.; Puchta, A.; Fleischer, J.; Noack, B.; Spiliopoulou, M.
2024. 2024 IEEE International Conference on Multisensor Fusion and Integration for Intelligent Systems (MFI), Pilsen, Czech Republic, 04-06 September 2024, Institute of Electrical and Electronics Engineers (IEEE). doi:10.1109/MFI62651.2024.10705783
Kader, H.; Ströbel, R.; Puchta, A.; Fleischer, J.; Noack, B.; Spiliopoulou, M.
2024. 2024 IEEE International Conference on Multisensor Fusion and Integration for Intelligent Systems (MFI), Pilsen, Czech Republic, 04-06 September 2024, Institute of Electrical and Electronics Engineers (IEEE). doi:10.1109/MFI62651.2024.10705783
Black Box Adversarial Reprogramming for Time Series Feature Classification in Ball Bearings’ Remaining Useful Life Classification
Bott, A.; Schreyer, F.; Puchta, A.; Fleischer, J.
2024. Machine Learning and Knowledge Extraction, 6 (3), 1969 – 1996. doi:10.3390/make6030097
Bott, A.; Schreyer, F.; Puchta, A.; Fleischer, J.
2024. Machine Learning and Knowledge Extraction, 6 (3), 1969 – 1996. doi:10.3390/make6030097
Supervised Domain Adaptation for Surface Defect Detection Leveraging Partial Data Availability
Heider, I.; Baumgärtner, J.; Bartz, P.; Puchta, A.; Fleischer, J.
2024. 2024 IEEE 20th International Conference on Automation Science and Engineering (CASE), Bari, 28th August 2024 - 1st September 2024, 4134–4139, Institute of Electrical and Electronics Engineers (IEEE). doi:10.1109/CASE59546.2024.10711640
Heider, I.; Baumgärtner, J.; Bartz, P.; Puchta, A.; Fleischer, J.
2024. 2024 IEEE 20th International Conference on Automation Science and Engineering (CASE), Bari, 28th August 2024 - 1st September 2024, 4134–4139, Institute of Electrical and Electronics Engineers (IEEE). doi:10.1109/CASE59546.2024.10711640
Training and validation dataset 3 of milling processes for time series prediction
Ströbel, R.; Mau, M.; Kader, H.; Erd, D.; Bless, D.; Deucker, S.; Puchta, A.; Fleischer, J.; Noack, B.
2024, Juni 18. doi:10.35097/feFwILjideOropmh
Ströbel, R.; Mau, M.; Kader, H.; Erd, D.; Bless, D.; Deucker, S.; Puchta, A.; Fleischer, J.; Noack, B.
2024, Juni 18. doi:10.35097/feFwILjideOropmh
Improving Time Series Regression Model Accuracy via Systematic Training Dataset Augmentation and Sampling
Ströbel, R.; Mau, M.; Puchta, A.; Fleischer, J.
2024. Machine Learning and Knowledge Extraction, 6 (2), 1072–1086. doi:10.3390/make6020049
Ströbel, R.; Mau, M.; Puchta, A.; Fleischer, J.
2024. Machine Learning and Knowledge Extraction, 6 (2), 1072–1086. doi:10.3390/make6020049
Autonome Modellierung von Maschinenverhalten – Ansatz für die autonome Modellierung des dynamischen Verhaltens von Fräsmaschinen und Potenziale dieses Ansatzes in der Industrie
Oexle, F.; Netzer, M.; Deiters, L.; Puchta, A.; Fleischer, J.
2024. ZWF – Zeitschrift für wirtschaftlichen Fabrikbetrieb, 119 (5), 318–323. doi:10.1515/zwf-2024-1054
Oexle, F.; Netzer, M.; Deiters, L.; Puchta, A.; Fleischer, J.
2024. ZWF – Zeitschrift für wirtschaftlichen Fabrikbetrieb, 119 (5), 318–323. doi:10.1515/zwf-2024-1054
Concept for Individual and Lifetime-Adaptive Modeling of the Dynamic Behavior of Machine Tools
Oexle, F.; Heimberger, F.; Puchta, A.; Fleischer, J.
2024. Machines, 12 (2), Art.-Nr.: 123. doi:10.3390/machines12020123
Oexle, F.; Heimberger, F.; Puchta, A.; Fleischer, J.
2024. Machines, 12 (2), Art.-Nr.: 123. doi:10.3390/machines12020123
Towards Reconfigurable Cyber-Physical-Human Systems: Leveraging Mixed Reality and Digital Twins to integrate Human Operations
Mayer, A.; Kastner, K.; Mühlbeier, E.; Chardonnet, J.-R.; Reichwald, J.; Puchta, A.; Fleischer, J.; Ovtcharova, J.
2024. Procedia CIRP, 130, 524 – 531. doi:10.1016/j.procir.2024.10.124
Mayer, A.; Kastner, K.; Mühlbeier, E.; Chardonnet, J.-R.; Reichwald, J.; Puchta, A.; Fleischer, J.; Ovtcharova, J.
2024. Procedia CIRP, 130, 524 – 531. doi:10.1016/j.procir.2024.10.124
Ai business models in manufacturing – characteristics of ai business models in manufacturing; [Charakteristiken von KI-Geschäftsmodellen in der Produktion KI-Geschäftsmodelle in der Produktion]
Heider, I.; Frisch, M.; Sawodny, J.; Puchta, A.; Fleischer, J.
2024. wt Werkstattstechnik online, 114 (07-08), 445 – 451. doi:10.37544/1436-4980-2024-07-08-65
Heider, I.; Frisch, M.; Sawodny, J.; Puchta, A.; Fleischer, J.
2024. wt Werkstattstechnik online, 114 (07-08), 445 – 451. doi:10.37544/1436-4980-2024-07-08-65
Milling using two mechatronically coupled robots
Goebels, M.; Baumgärtner, J.; Fuchs, T.; Mühlbeier, E.; Puchta, A.; Fleischer, J.
2024. Procedia CIRP, 130, 867–872. doi:10.1016/j.procir.2024.10.177
Goebels, M.; Baumgärtner, J.; Fuchs, T.; Mühlbeier, E.; Puchta, A.; Fleischer, J.
2024. Procedia CIRP, 130, 867–872. doi:10.1016/j.procir.2024.10.177
Towards a Testing Framework for Machine Learning Model Deployment in Manufacturing Systems
Heider, I.; Baumgärtner, J.; Bott, A.; Ströbel, R.; Puchta, A.; Fleischer, J.
2024. 10th CIRP Conference on Assembly Technology and Systems (CIRP CATS 2024) Hrsg.: Fleischer , Jürgen; Jörg, Krüger, 127, 122–128. doi:10.1016/j.procir.2024.07.022
Heider, I.; Baumgärtner, J.; Bott, A.; Ströbel, R.; Puchta, A.; Fleischer, J.
2024. 10th CIRP Conference on Assembly Technology and Systems (CIRP CATS 2024) Hrsg.: Fleischer , Jürgen; Jörg, Krüger, 127, 122–128. doi:10.1016/j.procir.2024.07.022
Sensor- and Data-Supported Sustainable Manufacturing
Fleischer, J.; Hansjosten, M.; Sawodny, J.; Puchta, A.; Gönnheimer, P.
2024. Encyclopedia of Sustainable Technologies, 648–662, Elsevier. doi:10.1016/B978-0-323-90386-8.00128-5
Fleischer, J.; Hansjosten, M.; Sawodny, J.; Puchta, A.; Gönnheimer, P.
2024. Encyclopedia of Sustainable Technologies, 648–662, Elsevier. doi:10.1016/B978-0-323-90386-8.00128-5
Camera Placement Optimization for a Novel Modular Robot Tracking System
Baumgärtner, J.; Bertschinger, B.; Hoffmann, K.; Puchta, A.; Sawodny, O.; Reichelt, S.; Fleischer, J.
2023. 2023 IEEE SENSORS, Vienna, Austria, 29 October 2023 - 01 November 2023, Institute of Electrical and Electronics Engineers (IEEE). doi:10.1109/SENSORS56945.2023.10324941
Baumgärtner, J.; Bertschinger, B.; Hoffmann, K.; Puchta, A.; Sawodny, O.; Reichelt, S.; Fleischer, J.
2023. 2023 IEEE SENSORS, Vienna, Austria, 29 October 2023 - 01 November 2023, Institute of Electrical and Electronics Engineers (IEEE). doi:10.1109/SENSORS56945.2023.10324941
KI-Transferzentrum für die Industrie
Hansjosten, M.; Oexle, F.; Gönnheimer, P.; Heider, I.; Puchta, A.; Fleischer, J.
2023. wt Werkstattstechnik online
Hansjosten, M.; Oexle, F.; Gönnheimer, P.; Heider, I.; Puchta, A.; Fleischer, J.
2023. wt Werkstattstechnik online
Increasing Robot Precision by Stroke Division
Baumgärtner, J.; Puchta, A.; Bertschinger, B.; Kanagalingam, G.; Sawodny, O.; Reichelt, S.; Fleischer, J.
2023. 2023 27th International Conference on Methods and Models in Automation and Robotics (MMAR), Międzyzdroje, Poland, 22-25 August 2023. Ed.: A. Bartoszewicz, 205–210, Institute of Electrical and Electronics Engineers (IEEE). doi:10.1109/MMAR58394.2023.10242468
Baumgärtner, J.; Puchta, A.; Bertschinger, B.; Kanagalingam, G.; Sawodny, O.; Reichelt, S.; Fleischer, J.
2023. 2023 27th International Conference on Methods and Models in Automation and Robotics (MMAR), Międzyzdroje, Poland, 22-25 August 2023. Ed.: A. Bartoszewicz, 205–210, Institute of Electrical and Electronics Engineers (IEEE). doi:10.1109/MMAR58394.2023.10242468
Auto-identification of dynamic axis models in machine tools
Puchta, A.; Riegel, V.; Barton, D.; Fleischer, J.
2023. 16th CIRP Conference on Intelligent Computation in Manufacturing Engineering Hrsg.: Teti, Prof Roberto, 118, 175–180. doi:10.1016/j.procir.2023.06.031
Puchta, A.; Riegel, V.; Barton, D.; Fleischer, J.
2023. 16th CIRP Conference on Intelligent Computation in Manufacturing Engineering Hrsg.: Teti, Prof Roberto, 118, 175–180. doi:10.1016/j.procir.2023.06.031
Software-Defined Manufacturing for the Entire Life Cycle at Different Levels of Production
Behrendt, S.; Martin, M.; Puchta, A.; Ströbel, R.; Fisel, J.; May, M.; Gönnheimer, P.; Fleischer, J.; Lanza, G.
2023. Advances in Automotive Production Technology – Towards Software-Defined Manufacturing and Resilient Supply Chains : Stuttgart Conference on Automotive Production (SCAP2022). Ed.: N. Kiefl, 25–34, Springer International Publishing. doi:10.1007/978-3-031-27933-1_3
Behrendt, S.; Martin, M.; Puchta, A.; Ströbel, R.; Fisel, J.; May, M.; Gönnheimer, P.; Fleischer, J.; Lanza, G.
2023. Advances in Automotive Production Technology – Towards Software-Defined Manufacturing and Resilient Supply Chains : Stuttgart Conference on Automotive Production (SCAP2022). Ed.: N. Kiefl, 25–34, Springer International Publishing. doi:10.1007/978-3-031-27933-1_3
Model-Based Diagnosis of Feed Axes with Contactless Current Sensing
Hansjosten, M.; Bott, A.; Puchta, A.; Gönnheimer, P.; Fleischer, J.
2023. M. Liewald, T. Bauernhansl, H.-C. Möhring & A. Verl (Hrsg.), Production at the Leading Edge of Technology: Proceedings of the 12th Concress of the German Academic Association for Production Technology (WGP), University of Stuttgart, October 2022. Hrsg.: Mathias Liewald, Thomas Bauernhansl, Hans-Christian Möhring, Alexander Verl, 314–323, Springer. doi:10.1007/978-3-031-18318-8_33
Hansjosten, M.; Bott, A.; Puchta, A.; Gönnheimer, P.; Fleischer, J.
2023. M. Liewald, T. Bauernhansl, H.-C. Möhring & A. Verl (Hrsg.), Production at the Leading Edge of Technology: Proceedings of the 12th Concress of the German Academic Association for Production Technology (WGP), University of Stuttgart, October 2022. Hrsg.: Mathias Liewald, Thomas Bauernhansl, Hans-Christian Möhring, Alexander Verl, 314–323, Springer. doi:10.1007/978-3-031-18318-8_33
Introduction of an industrial transfer learning use case systematization for machine tools
Netzer, M.; Michelberger, J.; Puchta, A.; Verl, A.; Fleischer, J.
2023. Procedia CIRP, 120, 398 – 403. doi:10.1016/j.procir.2023.09.009
Netzer, M.; Michelberger, J.; Puchta, A.; Verl, A.; Fleischer, J.
2023. Procedia CIRP, 120, 398 – 403. doi:10.1016/j.procir.2023.09.009
KI-Einsatz in KMU: Einstiegshürden ausräumen [Clearing entry hurdles for AI deployment in SMEs – Artificial intelligence for German SMEs]
Heider, I.; Yu, H.; Krischke, N.; Wirth, B.; Puchta, A.; Fleischer, J.
2023. wt Werkstattstechnik online, 113 (07-08), 282 – 287. doi:10.37544/1436-4980-2023-07-08-16
Heider, I.; Yu, H.; Krischke, N.; Wirth, B.; Puchta, A.; Fleischer, J.
2023. wt Werkstattstechnik online, 113 (07-08), 282 – 287. doi:10.37544/1436-4980-2023-07-08-16
Convolutional-Based Encoder–Decoder Network for Time Series Anomaly Detection during the Milling of 16MnCr5
Schlagenhauf, T.; Wolf, J.; Puchta, A.
2022. mdpi data, 7 (175), Article no: 175. doi:10.3390/data7120175
Schlagenhauf, T.; Wolf, J.; Puchta, A.
2022. mdpi data, 7 (175), Article no: 175. doi:10.3390/data7120175
Multivariate time series dataset of milling 16MnCr5 for anomaly detection
Schlagenhauf, T.; Wolf, J.; Puchta, A.
2022, Oktober 19. doi:10.5445/IR/1000151546
Schlagenhauf, T.; Wolf, J.; Puchta, A.
2022, Oktober 19. doi:10.5445/IR/1000151546
Process Segmented based Intelligent Anomaly Detection in Highly Flexible Production Machines under Low Machine Data Availability
Netzer, M.; Bach, J.; Puchta, A.; Gönnheimer, P.; Fleischer, J.
2022. Procedia CIRP, 107, 647–652. doi:10.1016/j.procir.2022.05.040
Netzer, M.; Bach, J.; Puchta, A.; Gönnheimer, P.; Fleischer, J.
2022. Procedia CIRP, 107, 647–652. doi:10.1016/j.procir.2022.05.040
Framework for the Application of Industry 4.0 in Lithium-Ion Battery Cell Production
Schmied, J.; Puchta, A.; Scharmann, T.; Töpper, H.-C.; Kampker, A.; Jürgen, F.; Dröder, K.; Daub, R.
2022. Proceedings of the Conference on Production Systems and Logistics, CPSL 17th - 20th May, Vancouver 2022, 151–160, Leibniz Universität Hannover. doi:10.15488/12168
Schmied, J.; Puchta, A.; Scharmann, T.; Töpper, H.-C.; Kampker, A.; Jürgen, F.; Dröder, K.; Daub, R.
2022. Proceedings of the Conference on Production Systems and Logistics, CPSL 17th - 20th May, Vancouver 2022, 151–160, Leibniz Universität Hannover. doi:10.15488/12168
Industrie 4.0 in der Batteriezellproduktion : Systematische Integration von Industrie 4.0 in der Batteriezellproduktion = Systemic integration of Industry 4.0 in battery cell production – Industry 4.0 in battery cell production
Puchta, A.; Schmied, J.; Scharmann, T.; Töpper, H.; Fleischer, J.; Kampker, A.; Dröder, K.; Daub, R.
2022. WT Werkstattstechnik, 112 (7-8), 496–500. doi:10.37544/1436-4980-2022-07-08-50
Puchta, A.; Schmied, J.; Scharmann, T.; Töpper, H.; Fleischer, J.; Kampker, A.; Dröder, K.; Daub, R.
2022. WT Werkstattstechnik, 112 (7-8), 496–500. doi:10.37544/1436-4980-2022-07-08-50
Modular and flexible Automation Middleware based on LabVIEW and OPC UA
Künzel, A.; Puchta, A.; Gönnheimer, P.; Fleischer, J.
2021. 9th Manufacturing Engineering Society International Conference (MESIC 2021) 23rd-25th June 2021, Gijόn, Spain, Art.Nr.: 012109, Institute of Physics Publishing Ltd (IOP Publishing Ltd)
Künzel, A.; Puchta, A.; Gönnheimer, P.; Fleischer, J.
2021. 9th Manufacturing Engineering Society International Conference (MESIC 2021) 23rd-25th June 2021, Gijόn, Spain, Art.Nr.: 012109, Institute of Physics Publishing Ltd (IOP Publishing Ltd)
Automated Identification of Parameters in Control Systems of Machine Tools
Gönnheimer, P.; Puchta, A.; Fleischer, J.
2021. B.-A. Behrens, A. Brosius, W. Hintze, S. Ihlenfeldt & J. P. Wulfsberg (Hrsg.), Production at the leading edge of technology – Proceedings of the 10th Congress of the German Academic Association for Production Technology (WGP), Dresden, 23-24 September 2020. Ed.: B.-A. Behrens, 568–577, Springer-Verlag. doi:10.1007/978-3-662-62138-7_57
Gönnheimer, P.; Puchta, A.; Fleischer, J.
2021. B.-A. Behrens, A. Brosius, W. Hintze, S. Ihlenfeldt & J. P. Wulfsberg (Hrsg.), Production at the leading edge of technology – Proceedings of the 10th Congress of the German Academic Association for Production Technology (WGP), Dresden, 23-24 September 2020. Ed.: B.-A. Behrens, 568–577, Springer-Verlag. doi:10.1007/978-3-662-62138-7_57
Seamless and modular architecture for autonomous machine tools
Fleischer, J.; Puchta, A.; Gönnheimer, P.
2021. Journal of Machine Engineering, 21 (3), 40–46. doi:10.36897/jme/141565
Fleischer, J.; Puchta, A.; Gönnheimer, P.
2021. Journal of Machine Engineering, 21 (3), 40–46. doi:10.36897/jme/141565