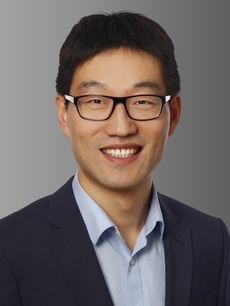
Dr.-Ing. Shun Yang
- Sino-European Innovation Director
- Bereich: Produktionssysteme
- Sprechstunden: nach Vereinbarung
- Raum: 008, Geb. 50.36
- Tel.: +49 176 3567 2636
- Fax: +49 721 608-45005
- Shun Yang ∂does-not-exist.partner kit edu
Campus Süd
Dr.-Ing. Shun Yang
Forschungs- und Arbeitsgebiete:
-
Standortgerechte Produktion
-
Smart Automation
-
Nachhaltige Produktion
-
Digitale Geschäftsmodelle
-
Qualitätssicherung
Allgemeine Aufgaben:
-
Sino-EU Innovationskooperation
-
Koordinator GAMI/KIT-China
Versuchsstände:
Dissertation:
Standortgerechte Einführungsstrategie von Smart Automation in Montagesystemen in China
Lebenslauf:
seit 03/2023 | Leiter von Sino-European Innovation |
09/2022 - 12/2022 | Gastwissenschaftler am Massachusetts Institute of Technolgoy (MIT), US |
04/2021 - 02/2023 | Post-Doc am KIT |
seit 04/2017 | Leiter von KIT China Branch |
01/2016 - 02/2023 | Wissenschaftlicher Mitarbeiter am Institut für Produktionstechnik (wbk) des Karlsruher Instituts für Technologie (KIT) |
09/2013 - 12/2015 | Studium des Produktionsoperation Management am KIT (M.Sc.) |
seit 04/2011 | Projektingenieur am GAMI |
04/2010 - 03/2011 | Forschungsaustausch am IWF an der TU-Braunschweig |
09/2007 - 03/2010 | Studium des Maschinenbaus am XAUAT, China (M.Sc.) |
09/2003 - 07/2007 | Studium des Maschinenbaus am XAUAT, China (B.Sc.) |
01/05/1985 | Geboren in Xi´an |
Veröffentlichungen
From cost to capability: Technology Multiplier in EV manufacturing strategy
Girke, R.; Schäfer, L.; Maier, T.; Stamer, F.; Yang, S.; Chun, J.-H.; Lanza, G.
2025. Journal of Manufacturing Systems, 82, 319–332. doi:10.1016/j.jmsy.2025.06.008
Girke, R.; Schäfer, L.; Maier, T.; Stamer, F.; Yang, S.; Chun, J.-H.; Lanza, G.
2025. Journal of Manufacturing Systems, 82, 319–332. doi:10.1016/j.jmsy.2025.06.008
Project selection and scheduling with multiplicative enhancement effects and delay risk: An application in intelligent manufacturing technologies
Liu, X.; Liang, J.; Zhang, Z.- hai; Yang, S.; Peukert, S.; Lanza, G.
2025. IISE Transactions, 57 (8), 873–889. doi:10.1080/24725854.2024.2374090
Liu, X.; Liang, J.; Zhang, Z.- hai; Yang, S.; Peukert, S.; Lanza, G.
2025. IISE Transactions, 57 (8), 873–889. doi:10.1080/24725854.2024.2374090
Sustainable Manufacturing for SMEs: An Agile Readiness Model of Decarbonization Through Theory and Practice
Tang, X.; Yang, S.; Qian, Y.; Thiede, S.
2025. Sustainable Manufacturing as a Driver for Growth – Proceedings of the 19th Global Conference on Sustainable Manufacturing, December 4–6, 2023, Buenos Aires, Argentina. Ed.: H. Kohl, 401 – 409, Springer Nature Switzerland. doi:10.1007/978-3-031-77429-4_44
Tang, X.; Yang, S.; Qian, Y.; Thiede, S.
2025. Sustainable Manufacturing as a Driver for Growth – Proceedings of the 19th Global Conference on Sustainable Manufacturing, December 4–6, 2023, Buenos Aires, Argentina. Ed.: H. Kohl, 401 – 409, Springer Nature Switzerland. doi:10.1007/978-3-031-77429-4_44
Effect of technology multiplier: A framework for analysis of innovation perspectives on production segment allocation
Stamer, F.; Girke, R.; Yang, S.; Chun, J.-H.; Lanza, G.
2024. CIRP Journal of Manufacturing Science and Technology, 55, 272–291. doi:10.1016/j.cirpj.2024.10.002
Stamer, F.; Girke, R.; Yang, S.; Chun, J.-H.; Lanza, G.
2024. CIRP Journal of Manufacturing Science and Technology, 55, 272–291. doi:10.1016/j.cirpj.2024.10.002
Final Report Sino-German Industry 4.0 Factory Automation Platform
Albers, A.; Ovtcharova, J.; Becker, J.; Lanza, G.; Zhang, W.; Zhang, T.; Qiao, F.; Ma, Y.; Wang, J.; Wu, Z.; Ehrmann, C.; Gönnheimer, P.; Behrendt, M.; Mandel, C.; Stürmlinger, T.; Klippert, M.; Kimmig, A.; Schade, F.; Yang, S.; Heider, I.; Xie, S.; Song, K.; Peng, J.; Goncalves, P.; Kampfmann, R.; Schlechtendahl, J.; Kattner, J.; Straub, C.; May, M.; Zhu, Z.; Bai, O.; Lin, Y.; Yang, Z.; Ding, L.; Rossol, A.-S.
2022. (J. Fleischer, Hrsg.), Karlsruher Institut für Technologie (KIT). doi:10.5445/IR/1000143693
Albers, A.; Ovtcharova, J.; Becker, J.; Lanza, G.; Zhang, W.; Zhang, T.; Qiao, F.; Ma, Y.; Wang, J.; Wu, Z.; Ehrmann, C.; Gönnheimer, P.; Behrendt, M.; Mandel, C.; Stürmlinger, T.; Klippert, M.; Kimmig, A.; Schade, F.; Yang, S.; Heider, I.; Xie, S.; Song, K.; Peng, J.; Goncalves, P.; Kampfmann, R.; Schlechtendahl, J.; Kattner, J.; Straub, C.; May, M.; Zhu, Z.; Bai, O.; Lin, Y.; Yang, Z.; Ding, L.; Rossol, A.-S.
2022. (J. Fleischer, Hrsg.), Karlsruher Institut für Technologie (KIT). doi:10.5445/IR/1000143693
Regionalized implementation strategy of smart automation within assembly systems in China. Dissertation
Yang, S.
2021, Dezember 6. Shaker Verlag. doi:10.5445/IR/1000140407
Yang, S.
2021, Dezember 6. Shaker Verlag. doi:10.5445/IR/1000140407
A Data-Driven Approach for Quality Analytics of Screwing Processes in a Global Learning Factory
Yang, S.; Liu, H.; Zhang, Y.; Arndt, T.; Hofmann, C.; Häfner, B.; Lanza, G.
2020. Procedia manufacturing, 45, 454–459. doi:10.1016/j.promfg.2020.04.052
Yang, S.; Liu, H.; Zhang, Y.; Arndt, T.; Hofmann, C.; Häfner, B.; Lanza, G.
2020. Procedia manufacturing, 45, 454–459. doi:10.1016/j.promfg.2020.04.052
Development of a regionalized implementation strategy for smart automation within assembly systems in China
Yang, S.; Schrage, J.; Haefner, B.; Lanza, G.
2019. Procedia CIRP, 80, 723–728. doi:10.1016/j.procir.2019.01.039
Yang, S.; Schrage, J.; Haefner, B.; Lanza, G.
2019. Procedia CIRP, 80, 723–728. doi:10.1016/j.procir.2019.01.039
Methodical approach for the development of a platform for the configuration and operation of turnkey production systems
Gönnheimer, P.; Kimmig, A.; Mandel, C.; Stürmlinger, T.; Yang, S.; Schade, F.; Ehrmann, C.; Klee, B.; Behrendt, M.; Schlechtendahl, J.; Fischer, M.; Trautmann, K.; Fleischer, J.; Lanza, G.; Ovtcharova, J.; Becker, J.; Albers, A.
2019. Procedia CIRP, 84, 880–885. doi:10.1016/j.procir.2019.04.260
Gönnheimer, P.; Kimmig, A.; Mandel, C.; Stürmlinger, T.; Yang, S.; Schade, F.; Ehrmann, C.; Klee, B.; Behrendt, M.; Schlechtendahl, J.; Fischer, M.; Trautmann, K.; Fleischer, J.; Lanza, G.; Ovtcharova, J.; Becker, J.; Albers, A.
2019. Procedia CIRP, 84, 880–885. doi:10.1016/j.procir.2019.04.260
A Method for Improving Production Management Training by Integrating an Industry 4.0 Innovation Center in China
Yang, S.; Hamann, K.; Haefner, B.; Wu, C.; Lanza, G.
2018. Procedia manufacturing, 23, 213–218. doi:10.1016/j.promfg.2018.04.019
Yang, S.; Hamann, K.; Haefner, B.; Wu, C.; Lanza, G.
2018. Procedia manufacturing, 23, 213–218. doi:10.1016/j.promfg.2018.04.019
Method for Developing an Implementation Strategy of Cyber-Physical Production Systems for Small and Medium-sized Enterprises in China
Yang, S.; Boev, N.; Haefner, B.; Lanza, G.
2018. Procedia CIRP, 76, 48–52. doi:10.1016/j.procir.2018.01.027
Yang, S.; Boev, N.; Haefner, B.; Lanza, G.
2018. Procedia CIRP, 76, 48–52. doi:10.1016/j.procir.2018.01.027
Laser-Strahlschmelzen - Technologie mit Zukunftspotenzial: Ein Handlungsleitfaden
Lanza, G.; Kopf, R.; Zaiß, M.; Stricker, N.; Eschner, N.; Jacob, A.; Yang, S.; Schönle, A.; Webersinke, L.; Wirsig, L.
2017. wbk Institut für Produktionstechnik
Lanza, G.; Kopf, R.; Zaiß, M.; Stricker, N.; Eschner, N.; Jacob, A.; Yang, S.; Schönle, A.; Webersinke, L.; Wirsig, L.
2017. wbk Institut für Produktionstechnik
A Flexible Simulation Support for Production Planning and Control in Small and Medium Enterprises
Yang, S.; Arndt, T.; Lanza, G.
2016. Procedia CIRP, 56, 389–394. doi:10.1016/j.procir.2016.10.062
Yang, S.; Arndt, T.; Lanza, G.
2016. Procedia CIRP, 56, 389–394. doi:10.1016/j.procir.2016.10.062