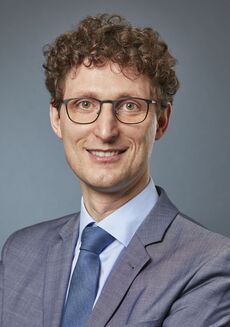
Prof. Dr.-Ing. Frederik Zanger
- Institutsleiter Fertigungs- und Werkstofftechnik
- Sprechstunden: nach Vereinbarung
- Raum: 119, Geb. 50.36
- Tel.: +49 721 608-42450
- Fax: +49 721 608-45005
- Frederik Zanger ∂does-not-exist.kit edu
Campus Süd
Prof. Dr.-Ing. Frederik Zanger
Kurzprofil:
Prof. Dr.-Ing. Frederik Zanger ist ein erfahrener Fertigungstechniker mit über 15 Jahren Forschungstätigkeit, spezialisiert auf Additive Fertigung, Zerspanung von Metallen, Simulation von Fertigungsprozessen und Digitalisierung von Prozessketten. Er hat die Forschungsgruppe Additive Fertigung am wbk Institut für Produktionstechnik des Karlsruher Instituts für Technologie (KIT) aufgebaut und hält seit 07/2023 den Lehrstuhl für Digitalisierung der Prozessentwicklung für die Additive Fertigung. Seine Expertise in der additiven Fertigung liegt in den Verfahren Powder Bed Fusion (Metalle), Directed Energy Deposition (Metalle), Binder Jetting (Metalle) und Vat Photopolymerization (Keramiken).
Forschungs- und Arbeitsgebiete:
Fertigungs- und Werkstofftechnik
Bereich Lehre:
Projektpraktikum Additive Fertigung: Entwicklung und Fertigung eines additiven Bauteils
Vorlesung Additive Fertigungsverfahren
Dissertation:
Lebenslauf
↵
seit 07/2023 | Inhaber der Professur für „Digitalisierung der Prozessentwicklung für die Additive Fertigung“ am wbk ‑ Institut für Produktionstechnik des Karlsruher Instituts für Technologie (KIT) |
03/2021 | Zertifikat Six Sigma Green Belt |
seit 03/2020 | CIRP Associate Member (Internationale Akademie der Produktionstechnik) |
10/2019 – 07/2023 | KIT-Industry Fellow: Forschungsgruppenleiter Additive Fertigung sowie Leiter Mechanische Fertigbearbeitung bei Edelstahl Rosswag |
03/2019 | Zertifikat Academic Leadership – Führung in der Wissenschaft |
11/2018 | Otto-Kienzle Gedenkmünze der WGP Wissenschaftliche Gesellschaft für Produktionstechnik für hervorragende Leistungen auf dem Gebiet der Fertigungstechnik |
seit 01/2017 | Koordinator des Forschungsschwerpunkts Additive Fertigung |
01/2015 - 12/2016 |
Koordinator des Forschungsschwerpunkts Mikroproduktion |
10/2014 - 09/2019 |
Vertreter des wissenschaftlichen Dienstes in der Studienkommission Maschinenbau |
10/2014 - 04/2018 |
Vertreter der wissenschaftlichen Mitarbeiter im Prüfungsausschuss Maschinenbau |
seit 04/2014 |
(Alumni-)Mitglied im Young Investigator Network (YIN) des KIT |
08/2013 - 07/2019 | Research Affiliate der CIRP (Nachwuchsnetzwerk der Internationalen Akademie der Produktionstechnik) |
05/2013 - 04/2019 |
DFG-Nachwuchsakademie mit dem Projekt Komplementärzerspanung - Simulationsgestützte Analyse eines in den Zerspanungsprozess integrierten Oberflächenverfestigungsverfahrens zur gezielten Erzeugung nanokristalliner Randschichten |
07/2013 | Dr.-Ing. Willy-Höfler-Doktorandenpreis für die beste Dissertation mit fertigungs-, mess- oder regelungstechnischer Zielsetzung |
01/2013 - 07/2019 | Lehrbeauftragter an der DHBW Karlsruhe |
12/2012 - 09/2017 | Geschäftsführer des Graduiertenkollegs 1483 (Prozessketten in der Fertigung: Wechselwirkung, Modellbildung und Bewertung von Prozesszonen) |
11/2012 - 10/2019 | Oberingenieur des Forschungsbereichs Fertigungs- und Werkstofftechnik am wbk - Institut für Produktionstechnik des Karlsruher Instituts für Technologie (KIT) |
02.11.2012 | Promotion: „Segmentspanbildung, Werkzeugverschleiß, Randschichtzustand und Bauteileigenschaften: Numerische Analysen zur Optimierung des Zerspanungsprozesses am Beispiel von Ti-6Al-4V“ |
01/2012 - 10/2012 | Gruppenleiter des Forschungsbereichs Fertigungs- und Werkstofftechnik am wbk - Institut für Produktionstechnik des Karlsruher Instituts für Technologie (KIT) |
10/2011 | Baden-Württemberg Zertifikat für Hochschuldidaktik |
seit 02/2009 | Koordinator der Forschungsschwerpunkte Virtuelle Produktion (6 Jahre), Mikroproduktion (2 Jahre) und Additive Fertigung (seit 01/2017) |
10/2007 – 11/2012 | Wissenschaftlicher Mitarbeiter in der Gruppe Fertigungs- und Werkstofftechnik am wbk - Institut für Produktionstechnik des Karlsruher Instituts für Technologie (KIT) |
06/2007 | Diplomarbeit am wbk – Institut für Produktionstechnik, Thema: „Mathematische Modellierung des Wärmeeintrags bei der Fräsbearbeitung von EN-GJL-260 Cr“ |
2002 – 2007 | Studium: Ingenieur-Pädagogik (Fachrichtung Maschinenbau und Mathematik) an der Universität Karlsruhe (TH) |
Veröffentlichungen
Maffia, S.; Krull, C.; Stittgen, T.; Wexel, H.; Zanger, F.; Koß, S.; Schleifenbaum, J. H.
2025. (S. Michelic & G. Mayer, Hrsg.) 17th CIRP Conference on Computer Aided Tolerancing (CAT2022) Hrsg.: Technisch-wissenschaftliches Organ der Montanuniversität Leoben, der ASMET Research GmbH (Austrian Society for Metallurgy; Materials) und des BVÖ (Bergmännischer Verband Österreichs), 170 (3), 179–187. doi:10.1007/s00501-025-01564-x
Schubert, J.; Friederich, P.; Burchard, B.; Zanger, F.
2024. Open Ceramics, 20, Art.-Nr.: 100705. doi:10.1016/j.oceram.2024.100705
Schubert, J.; Lehmann, C.-L.; Zanger, F.
2024. Ceramics International, 50 (23), 50948–50954. doi:10.1016/j.ceramint.2024.10.006
Lubkowitz, V.; Drechsel, K.; Schulze, V.; Zanger, F.
2024. Journal of Manufacturing Processes, 126, 348–357. doi:10.1016/j.jmapro.2024.07.118
Sen, S.; Mayer, D.; Fischer-Bühner, J.; Beckers, D.; Schubert, J.; Dietrich, S.; Kauffmann, A.; Zanger, F.
2024, September 25. Materials Science and Engineering Congress (MSE 2024), Darmstadt, Deutschland, 24.–26. September 2024
Fleischer, J.; Zanger, F.; Schulze, V.; Neumann, G.; Stricker, N.; Furmans, K.; Pfrommer, J.; Lanza, G.; Hansjosten, M.; Fischmann, P.; Dvorak, J.; Klein, J.-F.; Rauscher, F.; Ebner, A.; May, M. C.; Gönnheimer, P.
2024. at - Automatisierungstechnik, 72 (9), 861–874. doi:10.1515/auto-2024-0005
Heizmann, M.; Beyerer, J.; Dietrich, S.; Hoffmann, L.; Kaiser, J.-P.; Lanza, G.; Roitberg, A.; Stiefelhagen, R.; Stricker, N.; Wexel, H.; Zanger, F.
2024. at - Automatisierungstechnik, 72 (9), 829–843. doi:10.1515/auto-2024-0009
Ulff, N.; Leingang, E.; Schubert, J.; Zanger, F.
2024. Procedia CIRP, 124, 118 – 123. doi:10.1016/j.procir.2024.08.083
Frey, M.; Frankenhauser, M.; Schulze, V.; Zanger, F.
2024. Proceedings of the 35th Annual International Solid Freeform Fabrication Symposium. Ed.: J. Beaman, 720–731, University of Texas at Austin. doi:10.26153/tsw/58109
Schwalm, J.; Görtz, M.; Gonzalez, G.; Schulze, V.; Zanger, F.
2024. 7th CIRP Conference on Surface Integrity Hrsg.: Meyer, Daniel; Karpuschewski, Bernhard; Eich, Marco; Hettig, Matthias, 123, 179–184. doi:10.1016/j.procir.2024.05.033
Liao, Z.; Schoop, J. M.; Saelzer, J.; Bergmann, B.; Priarone, P. C.; Splettstößer, A.; Bedekar, V. M.; Zanger, F.; Kaynak, Y.
2024. CIRP Journal of Manufacturing Science and Technology, 50, 151 – 184. doi:10.1016/j.cirpj.2024.02.008
Wexel, H.; Kramer, S.; Schubert, J.; Schulze, V.; Zanger, F.
2024. Procedia CIRP, 123, 173–178. doi:10.1016/j.procir.2024.05.032
Wexel, H.; Fischmann, P.; Schubert, J.; Zanger, F.
2024. Procedia CIRP, Volume 127 Hrsg.: Fleischer, Jürgen; Jörg, Krüger, 127, 230–235. doi:10.1016/j.procir.2024.07.040
Kramer, S.; Jarwitz, M.; Schulze, V.; Zanger, F.
2024. Procedia CIRP, 124, 74 – 77. doi:10.1016/j.procir.2024.08.074
Lubkowitz, V.; Fayner, L.; Kramer, S.; Schulze, V.; Zanger, F.
2024. Procedia CIRP, 124, 135 – 140. doi:10.1016/j.procir.2024.08.086
Lubkowitz, V.; Scherer, T.; Schulze, V.; Zanger, F.
2024. Solid Freeform Fabrication 2023: Proceedings of the 34th Annual International Solid Freeform Fabrication Symposium (SFF2023). Hrsg.: J. Beaman, 514 – 524, Minerals, Metals and Materials Society (TMS). doi:10.26153/tsw/50967
Diaz Ocampo, D.; Aubart, D.; González, G.; Zanger, F.; Heizmann, M.
2024. Production Engineering, 18, 289–297. doi:10.1007/s11740-024-01266-2
Drechsel, K.; Lubkowitz, V.; Albrecht, L.; Schäfer, P.; Schneider, M.; Schulze, V.; Zanger, F.
2024. Powder Technology, 432, 119–153. doi:10.1016/j.powtec.2023.119153
Schubert, J.; Friederich, P.; Burchard, B.; Zanger, F.
2023, November 23. (T. Dahmen, T. Bernthaler, D. Britz & M. Stricker, Hrsg.), 1st Conference on Artificial Intelligence in Materials Science and Engineering (AI MSE 2023), Saarbrücken, Deutschland, 22.–23. November 2023
Ulff, N.; Schubert, J.; Zanger, F.
2023. Production at the Leading Edge of Technology: Proceedings of the 13th Congress of the German Academic Association for Production Technology (WGP), Freudenstadt, November 2023. Ed.: T. Bauernhansl, 747–756, Springer Nature Switzerland. doi:10.1007/978-3-031-47394-4_73
Schubert, J.; Lehmann, C.-L.; Schulze, V.; Zanger, F.
2023. Ceramic Applications, 11 (3), 12–16
Diaz Ocampo, D.; Koch, J.; González, G.; Zanger, F.; Heizmann, M.
2023. Production Engineering, 17 (5), 733–741. doi:10.1007/s11740-023-01200-y
Lubkowitz, V.; Schubert, J.; Zanger, F.
2023. EMO Hannover Journal, 2023 (1), S56-S58
Schubert, J.; Lehmann, C.-L.; Zanger, F.; Schulze, V.; Utsch, D.; Thielen, N.; Franke, J.
2023, Juni. 15th Internationaler MID-Kongress - Mechatronic Integrated Discourse (2023), Amberg, Deutschland, 21.–22. Juni 2023
Schwalm, J.; Mann, F.; González, G.; Zanger, F.; Schulze, V.
2023. 19th CIRP Conference on Modeling of Machining Operations Hrsg.: Schulze, Volker; Biermann, Dirk, 117, 110–115. doi:10.1016/j.procir.2023.03.020
Fischmann, P.; Schrauth, F.; Zanger, F., (2)
2023. CIRP Annals, 72 (1), 145–148. doi:10.1016/j.cirp.2023.04.018
Nagato, K.; Ozawa, T.; Neuenfeldt, M.; Zanger, F.; Zhao, M.; Schulze, V.
2023. Materials and Design, 227, Art.-Nr.: 111696. doi:10.1016/j.matdes.2023.111696
Niederhofer, P.; Henke, L.; Frie, D.; Neuenfeldt, M.; Zanger, F.
2023. steel research international, Art.-Nr.: 2200754. doi:10.1002/srin.202200754
Schulze, V.; Zanger, F.; Schubert, J.
2022
Fischmann, P.; Schulze, V.; Zanger, F.
2022. 22nd Machining Innovations Conference for Aerospace Industry 2022 (MIC 2022), November 30th and December 1st 2022, Hannover, Germany, 88–93, SSRN. doi:10.2139/ssrn.4259263
Drechsel, K.; Frey, M.; Schulze, V.; Zanger, F.
2022. M. Liewald, A. Verl, T. Bauernhansl & H.-C. Möhring (Hrsg.), Production at the Leading Edge of Technology Hrsg.: Liewald, Matthias; Verl, Alexander; Bauernhansl, Thomas; Möhring, Hans-Christian. Proceedings of the 12th Congress of the German Academic Association for Production Technology (WGP) Stuttgart, Deutschland, 12.10.2022–13.10.2022, 366–375, Springer. doi:10.1007/978-3-031-18318-8_38
Schubert, J.; Rosen, M.; Zanger, F.
2022. B.-A. Behrens, A. Brosius, W.-G. Drossel, W. Hintze, S. Ihlenfeldt & P. Nyhuis (Hrsg.), Production at the Leading Edge of Technology : Proceedings of the 11th Congress of the German Academic Association for Production Technology (WGP), Dresden, September 2021. Ed. by Bernd-Arno Behrens, Alexander Brosius, Welf-Guntram Drossel, Wolfgang Hintze, Steffen Ihlenfeldt, Peter Nyhuis, 339–348, Springer International Publishing. doi:10.1007/978-3-030-78424-9_38
Rosen, M.; Klaiber, M.; Schubert, J.; Schulze, V.; Zanger, F.
2022. Zeitschrift für wirtschaftlichen Fabrikbetrieb (ZWF), 2022 (7-8), 461–466. doi:10.1515/zwf-2022-1095
Drechsel, K.; Schulze, V.; Zanger, F.
2022. Additive Fertigung : Werkstoffe - Prozesse - Wärmebehandlung = Additive Manufacturing : Materials – Processes - Heat Treatment (AWT 2022), Bremen, 29.-30. Juni 2022, 151–160, Arbeitsgemeinschaft Wärmebehandlung und Werkstofftechnik e. V
Pachnek, F.; González, G.; Diaz Ocampo, D.; Heizmann, M.; Zanger, F.
2022. Procedia CIRP, 108, 188–193. doi:10.1016/j.procir.2022.03.033
Schwalm, J.; Mann, F.; Gerstenmeyer, M.; Zanger, F.; Schulze, V.
2022. Procedia CIRP, 108, 240–245. doi:10.1016/j.procir.2022.03.042
Diaz Ocampo, D.; Heizmann, M.; Pachnek, F.; Kübler-Tesch, C.; Zanger, F.
2022. wt Werkstattstechnik online, 112 (11-12), 779–782. doi:10.37544/1436-4980-2022-11-12-53
Schubert, J.; End, Y.; Rosen, M.; Zanger, F.; Schulze, V.
2022. 5th International Conference on Hybrid Materials and Structures (2022), Leoben, Österreich, 20.–22. Juli 2022
Schwalm, J.; Gerstenmeyer, M.; Zanger, F.; Schulze, V.
2022. wt Werkstattstechnik online, 2022 (1), 22–27. doi:10.37544/1436-4980-2022-01-02-26
Schubert, J.; End, Y.; Schulze, V.; Zanger, F.
2022. Procedia CIRP, 10th CIRP Global Web Conference – Material Aspects of Manufacturing Processes, 115, 18–23. doi:10.1016/j.procir.2022.10.043
Lubkowitz, V.; Fischmann, P.; Schulze, V.; Zanger, F.
2022. 12TH CIRP CONFERENCE ON PHOTONIC TECHNOLOGIES (LANE 2022), 111, 87–91. doi:10.1016/j.procir.2022.08.136
Schubert, J.; Weisser, P.; Rosen, M.; Zanger, F.; Schulze, V.
2022. Chemie-Ingenieur-Technik, 94 (7), 967–974. doi:10.1002/cite.202100208
Schwalm, J.; Gerstenmeyer, M.; Zanger, F.; Schulze, V.
2022. WT Werkstattstechnik, 112 (1-2), 22–27. doi:10.37544/1436-4980-2021-1-2-26
Lubkowitz, V.; Reothia, N.; Zanger, F.
2021. New production technologies in aerospace industry : proceedings 2021 : MIC2021, 21st Machining Innovations Conference for Aerospace Industry :Hanover, December 1st and 2nd 2021. Ed.: Berend Denkena, 50–55, TEWISS Verlag. doi:10.2139/ssrn.3922719
Neuenfeldt, M.; Zanger, F.; Schulze, V.
2021. MM Science Journal, 2021 (November), 5030–5037. doi:10.17973/MMSJ.2021_11_2021148
Diaz Ocampo, D.; Gonzalez, G.; Zanger, F.; Heizmann, M.
2021. Technisches Messen, 88 (S1), S37–S41. doi:10.1515/teme-2021-0059
Schulze, V.; Lanza, G.; Zanger, F.; Gartner, P.; Fischmann, P.
2021, Juli
Graf, G.; Neuenfeldt, M.; Müller, T.; Fischer-Bühner, J.; Beckers, D.; Donisi, S.; Zanger, F.; Schulze, V.
2021. Advanced Materials Research, 2021 (1161), 27–36. doi:https://doi.org/10.4028/www.scientific.net/AMR.1161.27
González, G.; Schwär, D.; Segebade, E.; Heizmann, M.; Zanger, F.
2021. 18th CIRP Conference on Modeling of Machining Operations (CMMO), Ljubljana, Slovenia, June 15-17, 2021. Ed.: E. Govekar, 276–280, Elsevier. doi:10.1016/j.procir.2021.09.047
Lubkowitz, V.; Alber, J.; Zanger, F.
2021. Materials, 14 (21), 6665. doi:10.3390/ma14216665
Graf, G.; Nouri, N.; Dietrich, S.; Zanger, F.; Schulze, V.
2021. Materials, 14 (15), Art.-Nr.: 4251. doi:10.3390/ma14154251
Schwalm, J.; Liu, Y.; Söllner, Y.; Gerstenmayer, M.; Zanger, F.; Schulze, V.
2020. wt Werkstattstechnik online, 110 (11-12), 743–747. doi:10.37544/1436-4980-2020-11-12-7
Schulze, V.; Zanger, F.; Stampfer, B.; Seewig, J.; Uebel, J.; Zabel, A.; Wolter, B.; Böttger, D.
2020. Technisches Messen, 87 (11), 661–673. doi:10.1515/teme-2020-0044
Schwär, D.; González, G.; Segebade, E.; Zanger, F.; Heizmann, M.
2020. Technisches Messen. doi:10.1515/teme-2020-0056
Schwär, D.; Kunz, A.; Dehen, S.; Zanger, F.; Puente León, F.
2020. Technisches Messen, 87 (s1), s22–s27. doi:10.1515/teme-2020-0039
Neuenfeldt, M.; Zanger, F.; Schulze, V.
2020. HTM Journal of Heat Treatment and Materials, 2020 (3), 192–203. doi:10.3139/105.110411
Graf, G.; Leoni, M.; Müller, T.; Fischer-Bühner, J.; Frey, M.; Beckers, D.; Donisi, S.; Zanger, F.; Schulze, V.
2020. Holistic innovation in Additive Manufacturing
González, G.; Plogmeyer, M.; Zanger, F.; Biehl, S.; Bräuer, G.; Schulze, V.
2020. 5th CIRP Conference on Surface Integrity (CSI 2020), 1st E-Conference, 1 - 5 June 2020. Ed.: Pedro J. Arrazola, 176–180, Elsevier. doi:10.1016/j.procir.2020.02.113
Stampfer, B.; Böttger, D.; Gauder, D.; Zanger, F.; Häfner, B.; Straß, B.; Wolter, B.; Lanza, G.; Schulze, V.
2020. 5th CIRP Conference on Surface Integrity (CSI 2020), 1st E-Conference, 1 - 5 June 2020. Ed.: Pedro J. Arrazola, 83–88, Elsevier. doi:10.1016/j.procir.2020.02.067
Schwalm, J.; Gerstenmeyer, M.; Zanger, F.; Schulze, V.
2020. 5th CIRP Conference on Surface Integrity (CSI 2020), 1st E-Conference, 1 - 5 June 2020. Ed.: Pedro J. Arrazola, 89–94, Elsevier. doi:10.1016/j.procir.2020.02.035
Dehen, S.; Segebade, E.; Gerstenmeyer, M.; Zanger, F.; Schulze, V.
2020. 5th CIRP Conference on Surface Integrity (CSI 2020), 1st E-Conference, 1 - 5 June 2020. Ed.: Pedro J. Arrazola, 95–100, Elsevier. doi:10.1016/j.procir.2020.02.024
Stampfer, B.; Zanger, F.; Schulze, V.
2019. R. Schmitt & G. Schuh (Hrsg.), Advances in production research : proceedings of the 8th Congress of the German Academic Association for Production Technology (WGP), Aachen, November 19-20, 2018. Eds.: Robert Schmitt, Günther Schuh, 541–550, Springer International Publishing. doi:10.1007/978-3-030-03451-1_53
Neuenfeldt, P.; Kacaras, A.; Zanger, F.; Schulze, V.
2019. K. wbk Institute of Production Science (Hrsg.), Symposium Mechanical Surface Treatment 2019 : 8th Workshop Machine Hammer Peening : 22th - 23rd October 2019, Karlsruhe. Hrsg.: Volker Schulze, 138–149, wbk Institut für Produktionstechnik
Klose, J.; Zanger, F.; Schulze, V.
2019. International Conference on Gears 2019. 3rd International Conference on High Performance Plastic Gears 2019. 3rd International Conference on Gear Production 2019 : Garching/Munich, Germany September 18 – 20, 2019. Hrsg.: VDI Wissensforum GmbH, 1579–1590, VDI Verlag
Zapf, M.; Klose, J.; Zanger, F.; Schulze, V.
2019. International Conference on Gears 2019. 3rd International Conference on High Performance Plastic Gears 2019. 3rd International Conference on Gear Production 2019 : Garching/Munich, Germany September 18 – 20, 2019. Hrsg.: VDI Wissensforum GmbH, 1647–1658, VDI Verlag. doi:10.51202/9783181023556-1647
Gerstenmeyer, M.; Hartmann, J.; Zanger, F.; Schulze, V.
2019. HTM Journal of Heat Treatment and Materials, 74 (3), 181–190. doi:10.3139/105.110376
Graf, G.; Leoni, M.; Müller, T.; Fischer-Bühner, J.; Beckers, D.; Donisi, S.; Zanger, F.; Schulze, V.
2019. HI-AM 2020 — Holistic Innovation in Additive Manufacturing 2020, 25th - 26th June 2020
Vargas, B.; Klose, J.; Zanger, F.; Schulze, V.
2019. Forschungsvereinigung Antriebstechnik e.V. (FVA) (Hrsg.), 7th International Conference on Gear and Drivetrain Production, GETPRO, 19th – 20th March, 2019, Würzburg, 235–244
Helfrich, A.; Zanger, F.; Schulze, V.
2019. Continuous–discontinuous fiber-reinforced polymers : an integrated engineering approach. Ed.: Thomas Böhlke, 61–76, Carl Hanser Verlag
Imbrogno, S.; Umbrello, D.; Schulze, V.; Zanger, F.; Segebade, E.
2019. International journal of material forming. doi:10.1007/s12289-019-01515-1
González, G.; Segebade, E.; Zanger, F.; Schulze, V.
2019. Procedia CIRP, 82, 154–159. doi:10.1016/j.procir.2019.04.061
Vargas, B.; Zapf, M.; Klose, J.; Zanger, F.; Schulze, V.
2019. Procedia CIRP, 82, 455–460. doi:10.1016/j.procir.2019.04.039
Segebade, E.; Gerstenmeyer, M.; Dietrich, S.; Zanger, F.; Schulze, V.
2019. Procedia CIRP, 82, 113–118. doi:10.1016/j.procir.2019.04.043
Stampfer, B.; Golda, P.; Zanger, F.; Schießl, R.; Maas, U.; Schulze, V.
2019. Procedia CIRP, 82, 438–443. doi:10.1016/j.procir.2019.04.036
Kacaras, A.; Bächle, M.; Schwabe, M.; Zanger, F.; Puente León, F.; Schulze, V.
2019. Procedia CIRP, 81, 270–275. doi:10.1016/j.procir.2019.03.047
Zanger, F.; Kacaras, A.; Neuenfeldt, P.; Schulze, V.
2019. CIRP annals, manufacturing technology, 68 (1), 373–376. doi:10.1016/j.cirp.2019.04.086
Segebade, E.; Gerstenmeyer, M.; Zanger, F.; Schulze, V.
2018. Efficiency, Flexibility, Integration : Wiener Produktionstechnik Kongress 2018. Hrsg.: F. Bleicher, 113–118, New Academic Press
Gotze, E.; Postler, K.; Buschulte, S.; Zanger, F.; Schulze, V.
2018. 13th International Congress Molded Interconnect Devices (MID), Würzburg, Germany, 25-26 September 2018, 15–20, Institute of Electrical and Electronics Engineers (IEEE). doi:10.1109/ICMID.2018.8527061
Kacaras, A.; Gibmeier, J.; Zanger, F.; Schulze, V.
2018. (P. CIRP, Hrsg.) 4th CIRP Conference on Surface Integrity Hrsg.: CIRP, Procedia, 71, 221–226. doi:10.1016/j.procir.2018.05.067
Gerstenmeyer, M.; Segebade, E.; Fedder, G.; Zanger, F.; Schulze, V.
2018. 19. RoundTable Simulating Manufacturing : Tagungsband : 16.-17. Mai 2018, Congresszentrum Marburg / Simufact. Hrsg.: H. Schafstall, 32–45, Simufact Engineering
Stampfer, B.; Golda, P.; Zanger, F.; Schießl, R.; Maas, U.; Schulze, V.
2018. 68th CIRP General Assembly, International Academy for Production Engineering (2018), Tokio, Japan, 19.–25. August 2018
Segebade, E.; Kümmel, D.; Zanger, F.; Schneider, J.; Schulze, V.
2018. Procedia manufacturing, 18, 97–103. doi:10.1016/j.promfg.2018.11.013
Segebade, E.; Kümmel, D.; Zanger, F.; Schneider, J.; Schulze, V.
2018. Procedia CIRP, 71, 232–237. doi:10.1016/j.procir.2018.05.065
Gerstenmeyer, M.; Zanger, F.; Schulze, V.
2018. CIRP annals, manufacturing technology, 67 (1), 583–586. doi:10.1016/j.cirp.2018.04.103
Zanger, F.; Kacaras, A.; Bächle, M.; Schwabe, M.; Puente León, F.; Schulze, V.
2018. 51st CIRP Conference on Manufacturing Systems, CIRP CMS 2018; Stockholm Waterfront Congress CentreStockholm; Sweden; 16 May 2018 through 18 May 2018. Ed.: T. Kjellberg, 1421–1426, Elsevier. doi:10.1016/j.procir.2018.03.196
Götze, E.; Zanger, F.; Schulze, V.
2018. Proceedings of the 21st International ESAFORM Conference on Material Forming : ESAFORM 2018 : Palermo, Italy, 23-25 April 2018. Ed.: L. Fratini, Art.Nr. 070023. doi:10.1063/1.5034919
Gabsch, A.; Klotz, S.; Zanger, F.; Schulze, V.
2017. F. Vollertsen (Hrsg.), 8. Kolloquium Mikroproduktion : Fachbeiträge, Bremen, 27.-28. November 2017 / Hrsg.: F. Vollertsen, 149–154, Verlag BIAS
Segebade, E.; Klose, J.; Gerstenmeyer, M.; Zanger, F.; Schulze, V.
2017. I. S. C. for Shot Peening (Hrsg.), ICSP13 : 13th International Conference on Shot Peening : 18-21 September 2017, Montréal, Canada / organizing institution: Polytechnique Montréal: Proceedings, 219–224, [Verlag nicht ermittelbar]
Segebade, E.; Gerstenmeyer, M.; Zanger, F.; Schulze, V.
2017. massivUmformung, 2017, 56–59
Zanger, F.; Sellmeier, V.; Klose, J.; Bartkowiak, M.; Schulze, V.
2017. Procedia CIRP, 58, 222–227. doi:10.1016/j.procir.2017.03.216
Segebade, E.; Zanger, F.; Schulze, V.
2017. Spanende Fertigung. Hrsg.: Dirk Biermann, 79–86, Vulkan-Verlag
Zanger, F.; Bollig, P.; Schulze, V.
2017. (Elsevier, Hrsg.) Procedia CIRP, 58, 140–145. doi:10.1016/j.procir.2017.03.203
Götze, E.; Heinzel, Y.; Matuschka, B.; Zanger, F.; Schulze, V.; Rohde, M.; Krügelstein, A.; Franke, J.
2017. F. Vollertsen (Hrsg.), 8. Kolloquium Mikroproduktion : Fachbeiträge, Bremen, 27.-28. November 2017 / Hrsg.: F. Vollertsen, 129–134, Verlag BIAS
Götze, E.; Zanger, F.; Schulze, V.
2017. Proceedings of the Special Interest Group Meeting on Dimensional Accuracy and Surface Finish in Additive Manufacturing : October 10-11, 2017, Leuven, BE. Ed.: W. Dewulf, 99–103, European Society for Precision Engineering and Nanotechnology (euspen)
Schulze, V.; Zanger, F.; Bollig, P.; Segebade, E.; Gerstenmeyer, M.; Klotz, S.
2017. Moderne Zerspanungstechnologie : neue Entwicklungen und Trends aus Forschung und Praxis : Jahrbuch zum 3. Innovation Forum Zerspanungstechnolgie, 2019. Hrsg.: Bahman Azarhoushang, Hochschule Furtwangen
Segebade, E.; Gerstenmeyer, M.; Zanger, F.; Schulze, V.
2017. M. Wohlmuth & H. Schafstall (Hrsg.), 18. RoundTable Simulating Manufacturing : Tagungsband : 30. Mai-1. Juni 2017, Congresszentrum Marburg. Hrsg.: Michael Wohlmuth, Hendrik Schafstall, 116–127, Simufact Engineering GmbH
Gerstenmeyer, M.; Segebade, E.; Zanger, F.; Schulze, V.
2017. M. Wohlmuth (Hrsg.), 18. RoundTable Simulating Manufacturing : Tagungsband : 30. Mai-1. Juni 2017, Marburg. Hrsg.: Hendrik Schafstall, 180–189, Simufact Engineering GmbH
Klotz, S.; Zanger, F.; Sellmeier, V.; Schulze, V.
2017. Werkstatt und Betrieb, 2016, 62–65
Imbrogno, S.; Umbrello, D.; Segebade, E.; Fellmeth, A.; Gerstenmeyer, M.; Zanger, F.; Schulze, V.
2017. Proceedings of the 20th International ESAFORM Conference on Material Forming, ESAFORM 2017, Ireland, Dublin, 26th - 28th April 2017, American Institute of Physics (AIP). doi:10.1063/1.5008112
Gerstenmeyer, M.; Ort, B.-L.; Zanger, F.; Schulze, V.
2017. Procedia CIRP, 58, 55–60. doi:10.1016/j.procir.2017.03.185
Segebade, E.; Gerstenmeyer, M.; Zanger, F.; Schulze, V.
2017. Procedia CIRP, 73–78. doi:10.1016/j.procir.2017.03.195
Fellmeth, A.; Zanger, F.; Schulze, V.
2017. Procedia CIRP, 58, 104–109. doi:10.1016/j.procir.2017.03.201
Helfrich, A.; Klotz, S.; Zanger, F.; Schulze, V.
2017. Procedia CIRP, 66, 193–198. doi:10.1016/j.procir.2017.03.366
Klotz, S.; Lepold, A.; Zanger, F.; Schulze, V.
2017. Procedia CIRP, 62, 15–20. doi:10.1016/j.procir.2016.06.089
Zanger, F.; Gerstenmeyer, M.; Weule, H.
2017. CIRP annals, manufacturing technology, 66 (1), 81–84. doi:10.1016/j.cirp.2017.04.026
Bejnoud, F.; Zanger, F.; Schulze, V.
2016. 13th International Conference on High Speed Machining : Progress in High Speed Machining Technology, October 4-5, 2016, Metz, France., 6
Schulze, V.; Bollig, P.; Gerstenmeyer, M.; Segebade, E.; Zanger, F.
2016. mav Innovationsforum 2016, 1, 6
Matuschka, B.; Boev, N.; Zanger, F.; Schulze, V.
2016. WGP Congress 2016 : Selected, peer reviewed papers from the 2016 WGP Congress, September 5-6, 2016, Hamburg, Germany. Ed.: J. P. Wulfsberg, 173–180, Trans Tech Publications. doi:10.4028/www.scientific.net/AMR.1140.173
Bollig, P.; Wengle, D.; Schulze, V.; Zanger, F.
2016. Maschinenmarkt, 122, 32–35
Bollig, P.; Köhler, D.; Zanger, F.; Schulze, V.
2016. Procedia CIRP, 46, 115–118. doi:10.1016/j.procir.2016.03.186
Fleischer, J.; Schulze, V.; Klaiber, M.; Bauer, J.; Zanger, F.; Boev, N.; Leberle, U.; Spohrer, A.; Rothaupt, B.
2016. Procedia CIRP, 46, 226–229. doi:10.1016/j.procir.2016.03.183
Gerstenmeyer, M.; Zanger, F.; Schulze, V.
2016. Procedia CIRP, 45, 247–250. doi:10.1016/j.procir.2016.02.048
Segebade, E.; Zanger, F.; Schulze, V.
2016. Procedia CIRP, 45, 11–14. doi:10.1016/j.procir.2016.02.070
Schoop, J.; Ambrosy, F.; Zanger, F.; Schulze, V.; Jawahir, I. S.; Balk, T. J.
2016. Materials and manufacturing processes, 31 (7), 823–831. doi:10.1080/10426914.2015.1048467
Schoop, J.; Ambrosy, F.; Zanger, F.; Schulze, V.; Balk, T. J.; Jawahir, I. S.
2016. Journal of materials processing technology, 229, 614–621. doi:10.1016/j.jmatprotec.2015.10.002
Zanger, F.; Boev, N.; Schulze, V.
2015. (V. Schulze, Hrsg.) Procedia CIRP, 31, 88–93. doi:10.1016/j.procir.2015.03.022
Zanger, F.; Fellmeth, A.; Gerstenmeyer, M.; Schulze, V.
2015. (V. Schulze, Hrsg.) 15th CIRP Conference on Modelling of Machining Operations (15th CMMO) Hrsg.: Schulze, Volker, 31, 106–111. doi:10.1016/j.procir.2015.03.102
Bejnoud, F.; Zanger, F.; Schulze, V.
2015. Progress in Production Engineering. Hrsg.: Jens P. Wulfsberg, Benny Röhlig and Tobias Montag, 239–246. doi:10.4028/www.scientific.net/AMM.794.239
Ambrosy, F.; Zanger, F.; Schulze, V.
2015. CIRP annals, manufacturing technology, 64 (1), 69–72. doi:10.1016/j.cirp.2015.04.063
Klotz, S.; Zanger, F.; Schulze, V.
2014. New production technologies in aerospace industry : Machining Innovations Conference ; proceedings ; November 19th and 20th, 2014 in Hannover. Hrsg.: B. Denkena, 248–256, TEWISS - Technik und Wissen
Zanger, F.; Gerstenmeyer, M.
2014. WGP Congress 2014 : progress in production engineering ; selected, peer reviewed papers from the 2014 WGP Congress, September 9 - 10, 2014, Erlangen, Germany. Ed.: M. Merklein, 161–166, Trans Tech Publications. doi:10.4028/www.scientific.net/AMR.1018.161
Fleischer, J.; Schulze, V.; Zanger, F.; Leberle, U.; Boev, N.; Spohrer, A.
2014. VDI-Z, 156, 42–44
Zanger, F.; Boev, N.; Schulze, V.
2014. Procedia CIRP, 13, 114–119. doi:10.1016/j.procir.2014.04.020
Hoppen, P.; Zanger, F.; Schulze, V.
2014. Mikroproduktion, 2014, 58–62
Klotz, S.; Gerstenmeyer, M.; Zanger, F.; Schulze, V.
2014. Procedia CIRP, 13, 208–213. doi:10.1016/j.procir.2014.04.036
Ambrosy, F.; Zanger, F.; Schulze, V.; Jawahir, I.-S.
2014. Procedia CIRP, 13, 169–174. doi:10.1016/j.procir.2014.04.029
Schulze, V.; Zanger, F.; Boev, N.; Michna, J.; Maas, U.; Faltin, C.; Schneider, J.; Bollig, P.
2014. Advanced Engineering Materials, 16 (2), 137–141. doi:10.1002/adem.201300103
Schulze, V.; Zanger, F.; Deuchert, M.; Hoppen, P.
2013. S. Azcárate & S. Dimov (Hrsg.), International Conference on Multi-Material Micro Manufacture Hrsg.: Azcárate, Sabino; Dimov, Stefan, 225–228. doi:10.3850/978-981-07-7247-5-418
Schulze, V.; Michna, J.; Zanger, F.; Faltin, C.; Maas, U.; Schneider, J.
2013. HTM - journal of heat treatment and materials, 68 (1), 22–31. doi:10.3139/105.110177
Schulze, V.; Zanger, F.; Hoppen, P.
2013. Design education - growing our future : proceedings of the 15th International Conference on Engineering and Product Design Education, Dublin, Dublin Institute of Technology, Bolton Street, Dublin, Ireland, 5th-6th September 2013. Ed.: E. Bohemia, 58–63, The Design Society
Schulze, V.; Zanger, F.; Ambrosy, F.
2013. Progress in Production Engineering, WGP Kongress 2013, July 23-24, Erlangen, 109–115, Trans Tech Publications. doi:10.4028/www.scientific.net/AMR.769.109
Gerstenmeyer, M.; Klotz, S.; Zanger, F.; Schulze, V.
2013. Maschinenmarkt, 2013, 14–17
Schulze, V.; Arrazola, P.; Zanger, F.; Osterried, J.
2013. Procedia CIRP, 8, 45–50. doi:10.1016/j.procir.2013.06.063
Schulze, V.; Zanger, F.; Boev, N.
2013. Procedia CIRP, 8, 246–251. doi:10.1016/j.procir.2013.06.097
Schulze, V.; Zanger, F.; Michna, J.; Lang, F.
2013. Procedia CIRP, 8, 33–38. doi:10.1016/j.procir.2013.06.061
Zanger, F.; Schulze, V.
2013. Procedia CIRP, 8, 157–162. doi:10.1016/j.procir.2013.06.082
Schulze, V.; Zanger, F.; Krauße, M.; Boev, N.
2013. Procedia CIRP, 8, 251–256. doi:10.1016/j.procir.2013.06.098
Schulze, V.; Zanger, F.; Klotz, S.
2013. 19. Symposium Verbundwerkstoffe und Werkstoffverbunde, 03.07.2013 - 05.07.2013, Karlsruhe, Deutschland, 961–970
Schulze, V.; Zanger, F.; Ambrosy, F.
2013. Key Engineering Materials, 554-557, 2009–2010. doi:10.4028/www.scientific.net/KEM.554-557.2009
Kümmel, J.; Poser, K.; Zanger, F.; Michna, J.; Schulze, V.
2013. Advances in Tribology, 2, 519686/1–10. doi:10.1155/2013/519686
Schulze, V.; Michna, J.; Zanger, F.; Faltin, C.; Maas, U.; Schneider, J.
2013. HTM - Journal of Heat Treatment and Materials, 68 (1), 22–31
Schulze, V.; Klotz, S.; Zanger, F.
2012. Spanende Fertigung : Prozesse, Innovationen, Werkstoffe ; [40 Jahre ISF]. Hrsg.: D. Biermann, 330–337, Vulkan-Verlag
Schulze, V.; Boev, N.; Zanger, F.
2012. Procedia CIRP, 4, 140–145. doi:10.1016/j.procir.2012.10.025
Schulze, V.; Zanger, F.
2012. Spanende Fertigung : Prozesse, Innovationen, Werkstoffe ; [40 Jahre ISF]. Hrsg.: D. Biermann, 51–58, Vulkan-Verlag
Schulze, V.; Boev, N.; Zanger, F.
2012. Procedia CIRP, 1 (1), 454–459. doi:10.1016/j.procir.2012.04.078
Schulze, V.; Hoffmeister, J.; Zanger, F.; Ambrosy, F.; Erz, A.
2012. euspen Topical Meeting: Structured & Freeform Surfaces, 05.12.2012 - 06.12.2012, Teddington, UK, 57–80, Veranstalter European Society for Precision Engineering & Nanotechnology
Schulze, V.; Ambrosy, F.; Zanger, F.
2012. Konstruktion, (11/12), 14–16
Schulze, V.; Osterried, J.; Strauß, T.; Zanger, F.
2012. HTM Journal of heat treatment and materials, 67 (6), 347–356
Schulze, V.; Osterried, J.; Meier, H.; Zanger, F.
2011. Advanced materials research, 223, 37–45. doi:10.4028/www.scientific.net/AMR.223.37
Schulze, V.; Michna, J.; Zanger, F.; Pabst, R.
2011. Advanced Materials Research, 223, 371–380. doi:10.4028/www.scientific.net/AMR.223.371
Schulze, V.; Zanger, F.; Michna, J.; Ambrosy, F.; Pabst, R.
2011. Advanced Materials Research, 223, 20–209. doi:10.4028/www.scientific.net/AMR.223.20
Schulze, V.; Zanger, F.
2011. Advanced Materials Research, 223, 535–544. doi:10.4028/www.scientific.net/AMR.223.535
Schulze, V.; Zanger, F.
2011. Procedia Engineering, 19, 306–311. doi:10.1016/j.proeng.2011.11.117
Zanger, F.; Autenrieth, H.; Hoffmeister, J.; Schulze, V.
2010. Graduiertenkolleg 1483 - Prozessketten in der Fertigung: Wechselwirkung, Modellbildung und Bewertung von Prozesszonen, Begleitband zur 1. jährlichen Klausurtagung 2010. Hrsg.: R. Pabst, 125–129, Shaker Verlag
Osterried, J.; Zanger, F.; Autenrieth, H.; Schulze, V.
2010. Graduiertenkolleg 1483 - Prozessketten in der Fertigung: Wechselwirkung, Modellbildung und Bewertung von Prozesszonen, Begleitband zur 1. jährlichen Klausurtagung 2010. Hrsg.: R. Pabst, 57–61, Shaker Verlag
Fleischer, J.; Pabst, R.; Zanger, F.
2008. Spanende Fertigung: Prozesse, Innovationen, Werkstoffe. Hrsg.: Klaus Weinert, 530–541, Vulkan-Verlag
Fleischer, J.; Pabst, R.; Zanger, F.
2008. Begleitband zum Fachgespräch Zerspanen im Modernen Produktionsprozess, Dortmund, 26.-27. Februar 2008, 233–243, ISF
Fleischer, J.; Pabst, R.; Zanger, F.
2008. Spanende Fertigung: Prozesse, Innovationen, Werkstoffe. Hrsg.: K. Weinert, 530–541, Vulkan-Verlag