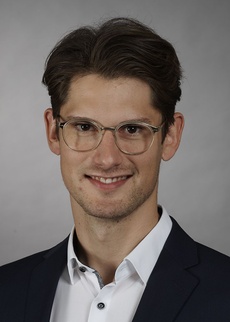
Dr.-Ing. Lucas Bretz
- General Manager of GAMI
- department: Production Systems
- office hours: to be agreed
- room: 108, Geb. 50.36
- lucas bretz ∂does-not-exist.silu asia
76131 Karlsruhe
Kaiserstraße 12
Dr.-Ing. Lucas Bretz
General Manager of Global Advanced Manufacturing Institute (GAMI)
Area of Research:
-
Quality assurance in lightweight construction
-
Machine Learning in Quality Assurance
-
Structural simulation (FEM)
-
Industry 4.0 maturity assessment
Curriculum Vitae:
since 07/2021 | General Manager of Global Advanced Manufacturing Institute (GAMI) |
06/2018 - 06/2021 | Research Associate at the Institute of Production Science (wbk) at Karlsruhe Institute of Technology (KIT) |
10/2017 - 03/2018 | Stay abroad at the Global Advanced Manufacturing Institute (GAMI) in Suzhou, China |
10/2012 - 04/2018 | Study of Mechanical Engineering at Karlsruhe Institute of Technology (KIT) |
15/12/1992 | Born in Dernbach, Westerwald |
Publications
Large Language Models for Robotics: A Systematic Literature Review on Prompt Engineering
Wolber, J.; Muyang, L.; Koch, D.; Bretz, L.; Lanza, G.; Baer, F.
2025. J. Min, W. Zhang, J. Fleischer & G. Lanza (Eds.), Sustainable Manufacturing Innovations: Focus on New Energy Vehicles, Production Robots, and Software-Defined Manufacturing: Proceedings of ICSM 2024, Shanghai, China, October 30-November 1, 2024 Hrsg.: Min, Junying; Zhang, Weimin; Fleischer, Jürgen; Lanza, Gisela, 201–213, Springer Nature Switzerland. doi:10.1007/978-3-031-84744-8
Wolber, J.; Muyang, L.; Koch, D.; Bretz, L.; Lanza, G.; Baer, F.
2025. J. Min, W. Zhang, J. Fleischer & G. Lanza (Eds.), Sustainable Manufacturing Innovations: Focus on New Energy Vehicles, Production Robots, and Software-Defined Manufacturing: Proceedings of ICSM 2024, Shanghai, China, October 30-November 1, 2024 Hrsg.: Min, Junying; Zhang, Weimin; Fleischer, Jürgen; Lanza, Gisela, 201–213, Springer Nature Switzerland. doi:10.1007/978-3-031-84744-8
Quality Function Deployment (QFD) for human-robot collaboration (HRC): Systematic selection of key performance indicators in HRC
Lv, M.; Xiao, I.; Mentenich, C.; Jia, Z.; Xie, N.; Zhang, W.; Bretz, L.
2024. Procedia CIRP, 130, 830 – 836. doi:10.1016/j.procir.2024.10.172
Lv, M.; Xiao, I.; Mentenich, C.; Jia, Z.; Xie, N.; Zhang, W.; Bretz, L.
2024. Procedia CIRP, 130, 830 – 836. doi:10.1016/j.procir.2024.10.172
In-line measurement of fiber mass fraction using Terahertz spectroscopy for a function-oriented quality assurance of glass fiber sheet molding compound
Bretz, L.; Niehues, G.; Funkner, S.; Bründermann, E.; Müller, A.-S.; Lanza, G.
2023. Measurement, 222, Art.-Nr.: 113560. doi:10.1016/j.measurement.2023.113560
Bretz, L.; Niehues, G.; Funkner, S.; Bründermann, E.; Müller, A.-S.; Lanza, G.
2023. Measurement, 222, Art.-Nr.: 113560. doi:10.1016/j.measurement.2023.113560
Function-oriented defect assessment in hybrid sheet molding compound tensile specimen using surrogate models
Bretz, L.; Koch, D.; Debowski, K.; Höger, K.; Lanza, G.
2023. Production Engineering, 17 (2), 223–236. doi:10.1007/s11740-022-01174-3
Bretz, L.; Koch, D.; Debowski, K.; Höger, K.; Lanza, G.
2023. Production Engineering, 17 (2), 223–236. doi:10.1007/s11740-022-01174-3
Function-oriented in-line quality assurance of hybrid sheet molding compound. PhD dissertation
Bretz, L.
2022, July 7. Shaker Verlag. doi:10.5445/IR/1000147740
Bretz, L.
2022, July 7. Shaker Verlag. doi:10.5445/IR/1000147740
Non-destructive measurement of fiber mass content of glass fiber sheet molding compound using Terahertz radiation
Bretz, L.; Häfner, B.; Lanza, G.
2021. Measurement, 168, Art.-Nr.: 108386. doi:10.1016/j.measurement.2020.108386
Bretz, L.; Häfner, B.; Lanza, G.
2021. Measurement, 168, Art.-Nr.: 108386. doi:10.1016/j.measurement.2020.108386
Direct Bundle Simulation approach for the compression molding process of Sheet Molding Compound
Meyer, N.; Schöttl, L.; Bretz, L.; Hrymak, A. N.; Kärger, L.
2020. Composites / A, 132, Article: 105809. doi:10.1016/j.compositesa.2020.105809
Meyer, N.; Schöttl, L.; Bretz, L.; Hrymak, A. N.; Kärger, L.
2020. Composites / A, 132, Article: 105809. doi:10.1016/j.compositesa.2020.105809
Comparison of anomaly detection capabilities of pulse phase thermography in transmission and reflection setup on Sheet Molding Compound
Bretz, L.; Wilke, M.; Häfner, B.; Lanza, G.
2020. Proceedings : 4th International Conference, Hybrid 2020, Materials and Structures, 28 - 29 April 2020, Web Conference, Germany. Ed.: J. M. Hausmann, 108–115, Deutsche Gesellschaft für Materialkunde e.V. (DGM)
Bretz, L.; Wilke, M.; Häfner, B.; Lanza, G.
2020. Proceedings : 4th International Conference, Hybrid 2020, Materials and Structures, 28 - 29 April 2020, Web Conference, Germany. Ed.: J. M. Hausmann, 108–115, Deutsche Gesellschaft für Materialkunde e.V. (DGM)
Design and quality assurance of intrinsic hybrid metal-CFRP lightweight structures
Bretz, L.; Günther, F.; Jost, H.; Schwarz, M.; Kretzschmar, V.; Pohl, M.; Weiser, L.; Häfner, B.; Summa, J.; Herrmann, H.-G.; Stommel, M.; Lanza, G.
2020. Proceedings : 4th International Conference, Hybrid 2020, Materials and Structures, 28 - 29 April 2020, Web Conference, Germany. Ed.: J. M. Hausmann, 144–159, Deutsche Gesellschaft für Materialkunde e.V. (DGM)
Bretz, L.; Günther, F.; Jost, H.; Schwarz, M.; Kretzschmar, V.; Pohl, M.; Weiser, L.; Häfner, B.; Summa, J.; Herrmann, H.-G.; Stommel, M.; Lanza, G.
2020. Proceedings : 4th International Conference, Hybrid 2020, Materials and Structures, 28 - 29 April 2020, Web Conference, Germany. Ed.: J. M. Hausmann, 144–159, Deutsche Gesellschaft für Materialkunde e.V. (DGM)
Process Simulation of Sheet Molding Compound (SMC) using Direct Bundle Simulation
Meyer, N.; Schöttl, L.; Bretz, L.; Hrymak, A.; Kärger, L.
2019, May 8. 12th International Conference on Composite Science and Technology (2019), Sorrento, Italy, May 8–10, 2019
Meyer, N.; Schöttl, L.; Bretz, L.; Hrymak, A.; Kärger, L.
2019, May 8. 12th International Conference on Composite Science and Technology (2019), Sorrento, Italy, May 8–10, 2019
Manufacturing uncertainties and resulting robustness of optimized patch positions on continuous-discontinuous fiber reinforced polymer structures
Fengler, B.; Schäferling, M.; Schäfer, B.; Bretz, L.; Lanza, G.; Häfner, B.; Hrymak, A.; Kärger, L.
2019. Hospital physician, 213, 47–57. doi:10.1016/j.compstruct.2019.01.063
Fengler, B.; Schäferling, M.; Schäfer, B.; Bretz, L.; Lanza, G.; Häfner, B.; Hrymak, A.; Kärger, L.
2019. Hospital physician, 213, 47–57. doi:10.1016/j.compstruct.2019.01.063
Funktionsorientierte Inline-Messtechnik von Faserverbunden : Integration von Messergebnissen in FE-Simulationen zur Inline-Funktionsbewertung von Faserverbunden
Bretz, L.; Haefner, B.; Lanza, G.
2019. wt Werkstattstechnik online, 109 (11-12), 816–821
Bretz, L.; Haefner, B.; Lanza, G.
2019. wt Werkstattstechnik online, 109 (11-12), 816–821
Evaluation of anomaly detection capabilities using a non-orthogonal camera angle in pulse-phase thermography
Bretz, L.; Hinze, T.; Häfner, B.; Lanza, G.
2019. Procedia CIRP, 85, 308–313. doi:10.1016/j.procir.2019.09.032
Bretz, L.; Hinze, T.; Häfner, B.; Lanza, G.
2019. Procedia CIRP, 85, 308–313. doi:10.1016/j.procir.2019.09.032