Projektbeschreibung InRePro: Inspektions- und Remanufacturingzelle mit prozessintegrierter Multi-Sensorik für einen digital-autonomen Fertigungsprozess
Um im Sinne der Kreislaufwirtschaft einen möglichst hohen Nutzungsgrad der vorhandenen Produktsubstanz in weiteren Lebenszyklen zu erreichen, ist es notwendig, werthaltige Komponenten (z.B. Rotor oder Gehäuse eines E-Motors) wiederaufzuarbeiten (Remanufacturing). Es ist daher erforderlich, in einer iterativen Prozesskette aus auftragenden und trennenden Fertigungsverfahren die Bauteilfunktion wiederherzustellen und diese idealerweise zu optimieren.
Herausforderungen, denen dabei begegnet werden muss, sind die folgenden:
• Erfassung ungewisser Produktzustände nach einer Nutzungsphase (z.B. Schädigungen) durch umfassende Inspektion
• Umsetzung einer bauteilindividuellen Prozesskette und Prozessführung
• Beherrschung von Unsicherheiten in der iterativen Prozesskette aus Trennen und Auftragen von metallischem Material
• Herstellung und Bewertung definierter Produkteigenschaften (z.B. tribologische Eigenschaften)
Um den Herausforderungen der Aufarbeitung von Gebrauchtprodukte zu begegnen, wird das im Folgenden beschriebene Großgerät beschafft, welches Teil der „Kreislauffabrik“ am KIT ist.
Die Remanufacturing-Zelle realisiert eine digital-autonome Prozesskette mit auftragenden und trennenden Fertigungsverfahren, die sich durch eine prozessintegrierte Multi-Sensorik auszeichnet. Diese prozessintegrierte Multi-Sensorik ermöglicht eine bauteilindividuelle Inspektion des Produktzustandes während - aber auch vor und nach - den Aufarbeitungsprozessen.
Inspektion ist dabei definiert als die Prüfung auf Konformität der maßgeblichen Merkmale eines Objekts durch Messung, Beobachtung oder Funktionsprüfung (nach [DIN-31051]). In der zu beschaffenden Fertigungszelle werden innerhalb von Prozessfolgen aus Trennen und Auftragen gebrauchte Bauteile überarbeitet und einem weiteren Lebenszyklus zugeführt. Die Aufarbeitung der Produkte ist dabei ein hochindividueller Prozess, der sich nach dem Bauteilzustand (individuelle Schädigung) sowie dem angestrebten Zielzustand des Bauteils richtet. Während des gesamten Aufarbeitungsprozesses ist es daher von großer Bedeutung, den aktuellen Produktzustand funktionsorientiert zu erfassen. Der Produktzustand vor, während und nach der Aufarbeitung ist dabei multi-skalig mit verschiedenen Auflösungen im Bauteilinneren und an der Bauteiloberfläche zu bestimmen. Das Großgerät umfasst hierfür eine breite Ausstattung an Sensorik, die verschiedene Mess- und Prüfgrößen erfassen kann. Die Sensorik kommt sowohl hauptzeitparallel (In-Process), also während der eigentlichen Prozessausführung (Zerspanen oder Auftragsschweißen), oder in den Prozessnebenzeiten (On-Machine aber Off-Process) zum Einsatz. Für die Erfassung innenliegender Defekte ist das System mit einem in den Strahlengang (On-Axis, In-Process) integrierten OCT (Optische Kohärenztomographie) ausgestattet. Durch das System ist die Schweißbahncharakteristik auch bei hohen Prozessgeschwindigkeiten in Echtzeit aufzuzeichnen. Dadurch kann hauptzeitparallel (In-Process) beim Laserauftragsschweißen das Prozessergebnis beobachtet werden. Hierdurch werden kurze Regelkreise ermöglicht und so eine, im Sinne der Aufarbeitung, optimale Prozessadaption gewährleistet.
Das auftragende Verfahren ist in dem Großgerät in einer Laserauftragsanlage umgesetzt. Herausforderung dieses Verfahrens ist die Wärmeeinflusszone, die prozessbedingt zustande kommt. Um die daraus möglicherweise resultierenden Risse durch eine geeignete Prozessführung zu vermeiden, sind verschiedene Messtechniken (In-Process) integriert. In den Schweißkopf des Auftragssystems selbst sind dafür entsprechende Sensoren (OCT, Quotienten-Pyrometer) integriert, die eine Überwachung des Schmelzbades ermöglichen. Außerdem wird die Prozesszone Off-Axis durch Erfassung der emittierten optischen Prozessstrahlung und Körperschall überwacht. Ein nachgeführter 3D-Laserscanner bietet zudem die Möglichkeit, das Auftragsergebnis direkt nach dem Auftragsprozess flächig geometrisch zu vermessen. Das System ermöglicht damit erstmals eine systematische Beobachtung und Ursachenforschung bei der Entstehung prozesstypischer Defekte.
Um das Trennen bzw. die spanende Bearbeitung in einem iterativen Prozess auch für hochindividuelle Bauteile und komplexe Strukturen zu ermöglichen, ist ein 5-Achs- Bearbeitungszentrum in das Großgerät integriert. Der Arbeitsraum ist von mehreren Seiten frei zugänglich, sodass während des Zerspanungsvorgangs (In-Process) neben klassischer Sensorik (Schnittkräfte, akustische Signale) weitere prozesscharakterisierende, robotergeführte Sensorik integriert werden kann.
Die Remanufacturing-Zelle soll durch einen Roboter zur autonomen Fertigung befähigt werden können, sodass Beladeluken vorzusehen sind und ein Bauteilhandling zwischen Bearbeitungszentrum und Laserauftragsanlage realisierbar wird. Die Erstinspektion von Bauteilen sowie die Bauteilabnahme sollen auf einem externen Rüstplatz möglich sein. Die entsprechende Steuerungsarchitektur und Sicherheitsmaßnamen sind darüber hinaus umzusetzen.
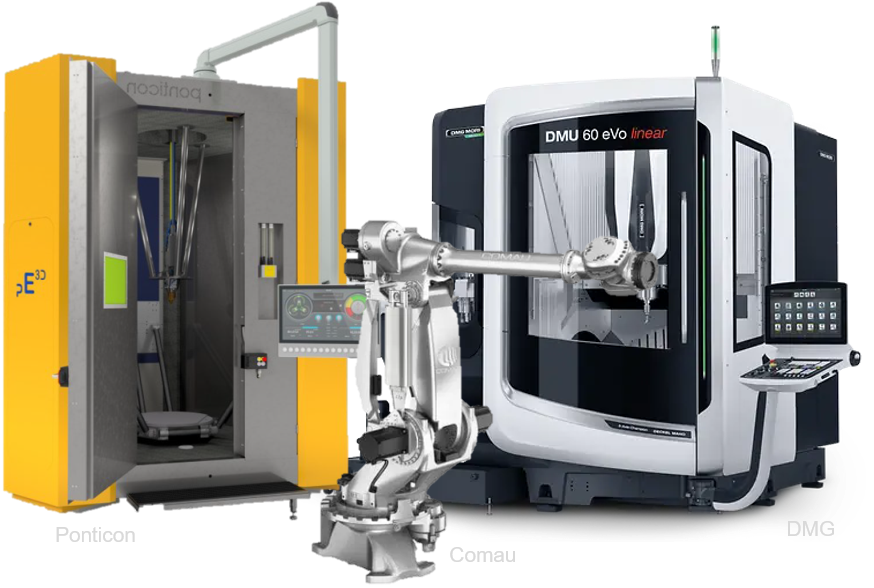
Fördervolumen: ca. 2 Mio. € |